Центробежно-ударная дробилка
Центробежно-ударный способ дробления известен достаточно давно и в последнее время находит все большее применение. Достаточно сказать, что первый патент на дробилку типа «камень о металл» получен Ц. Мелером в Германии еще в 1877 г.
Разработанная им конструкция предполагала несколько стадий дробления в одном аппарате. Для этого на одном валу было расположено нескольких ускорителей (роторов). Эта идея так и осталось нереализованной. В наши дни она представляется нерациональной из-за низкой надежности столь сложной конструктивной схемы.
Все известные на сегодняшний день промышленные центробежно-ударные дробилки имеют один ускоритель. Однороторный вариант схемы Ц. Мелера с открытым ротором, снабженным радиальными разгонными ребрами, использован для дробления «камень о металл» в дробилке «Торнадо» фирмы «Верко стил», США (рис.1). В центральной части сварного ускорителя предусмотрен распределительный конус. Цилиндрический корпус дробилки закрыт крышкой. Фиксация крышки на замках обеспечивает удобный доступ в дробильную камеру. Соосно ускорителю в крышке расположен загрузочный бункер и питающий патрубок. Брони крепятся к внутренней стенке корпуса.
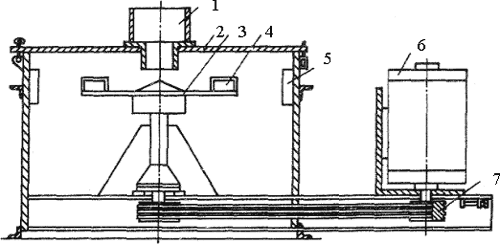
Рис. 1. Дробилка «Торнадо»
1 – питающий патрубок; 2 – крышка корпуса; 3 – ускоритель; 4 – разгонные ребра; 5 – брони;
6 – электродвигатель; 7 – клиноременная передача.
Кроме того, дробилки типа «камень о металл» с открытым ротором выпускала компания «Spokane Crasher», США. Ребра в ускорителе дробилки были съемными и выполнены из специальных сталей. С целью снижения износа ускорителя и повышения его динамической уравновешенности специалисты фирмы «Spokane Crasher» установили броневые плиты так, чтобы обеспечить при ударе прямой угол. Это было важно как для эффективности дробления, так и для снижения износа, поскольку минимизирует влияние рикошетов осколков. В дробилках с реверсивным приводом применялись броневые плиты симметричной угловой формы.
Дробилки «Spokane Crasher» типа «камень о металл» в свое время успешно заменили в США на предприятиях по производству строительных материалов конусные дробилки мелкого дробления. Однако в результате внедрения дробилки «Спокейн» эксплуатационные затраты на большинстве предприятий выросли в связи с тем, что открытый ускоритель с незащищенными ребрами и угловая отражательная футеровка подвержены высокому абразивному износу. Именно поэтому область применения дробилки типа «камень о металл» ограничена в основном переработкой строительных материалов низкой твердости, например, известняка и сланца.
Расширение сферы применения центробежно-ударной дробилки в 80-е годы произошло благодаря появлению компании «Barmac Associates», Новая Зеландия, и ее дробилки типа «камень о камень» с вертикальным валом. История дробилки и компании Barmac началась в 70-х годах ХХ века и связана с именем Джима Макдоналда (Jim McDonald). Он ведал работами в карьере в Kiwi Point недалеко от Веллингтона, столицы Новой Зеландии. В карьере брали щебень для городских дорог, включая защитное покрытие.
Новозеландские требования к кубовидности покрытия уже тогда были весьма жесткими. Чтобы соответствовать им, были необходимы ударные дробилки, однако стоимость эксплуатация на высоко абразивных материалах была слишком велика. Джим Макдоналд нашел способ защитить от абразивного износа вращающийся барабан (ускоритель), в котором разгоняется щебень в ударной дробилке. Для этого он применил сам щебень. Хотя идеи такого рода не новы, но в центробежно-ударных дробилках конструктивная концепция ускорителя, предложенная Джимом Макдоналдом, до сих пор остается непревзойденной.
Джим Макдонолд начал эксперименты в песочнице, на заднем дворе своего дома. Работы были продолжены вместе с коллегами в карьере. На основе проведенной работы Джим создал вертикальную ударную дробилку VSI (типа Canica), в которой дробимый материал служил защитой ускорителя и отбойной плиты. Результаты испытаний в Kiwi Point были превосходными, однако передний край ускорителя изнашивался очень быстро: закаленная сталь могла продержаться 2–3 часа. Решение – металлокерамический композит на основе карбида вольфрама и кобальта – подсказал Брайен Бэйтли (Bryan Baitley) на одной из конференций, после официальной части. Он и стал совладельцем интеллектуальной собственности новой компании «Barmac», названной по начальным буквам обоих изобретателей. Первый образец дробилки «Бармак Ротопактор» создан в 1975 г. В 1981 г. было продано около 40 образцов, к 1988 г. – более 800.
Принцип самофутеровки, принятый для защиты ускорителя и отражательной поверхности дробилки, предполагает закрытый ускоритель. Сегодня данное решение используют многие производителей центробежных дробилок. Способ формирования самофутеровки состоит в следующем (рис. 2). Перед началом работы новый ускоритель, штатно установленный в дробилку, приводится во вращение с номинальной или меньшей скоростью. В него понемногу подается доступный некрупный сыпучий материал, который образует на разгонных лопастях ускорителя защитный слой самофутеровки. Момент окончательного образования защитного слоя ускорителя песком определяется по тому, что песок появляется в разгрузочном отверстии дробилки. Затем подается горная масса, содержащая куски произвольной крупности, допустимой по техническим требованиям. Ее движение происходит во внутренних каналах ускорителя по ранее образованному слою песка.
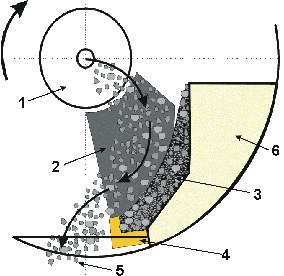
Рис. 2. Схема образования самофутеровки в ускорителе
1 – рассекатель; 2 – подкладной лист; 3 – самофутерющийся карман; 4 – твёрдосплавная лопатка; 5 – сход материала с ускорителя; 6 – корпус ускорителя
Остальные участки (поверхности ускорителя, незащищенные самофутеровкой) защищены износостойкими съемными деталями, выполненными из специальных материалов. Это кромка окна, кольцевые пластины ускорителя и его центральная зона, куда поступает питание. В современных дробилках обычно применяют сменные кольца, распределительный конус, подкладные листы из чугуна.
Применяемые марки чугунов отличаются особой твердостью (достигаемой за счет высокого содержания карбида хрома – до 30%), а также высокой прочностью и ударной вязкостью (их обеспечивают специальные легирующие добавки и режимы термообработки). Чугунный конус (колпак) устанавливают в ускорителе в центре на нижней кольцевой пластине. Он прикрывает шлицевое соединение ускорителя с приводным валом (крепится одним болтом) и встречает удар еще не закрученного потока горной массы.
Так называемые подкладные листы, которые представляют собой профилированные чугунные пластины, образуют «берега» потока горной массы и защищают от абразивного износа в каналах ускорителя внутреннюю поверхность верхней и нижней пластин. По совместительству пластины играют роль главных деталей силового каркаса ускорителя. Самофутеровка защищает от износа разгонные ребра силового каркаса, то есть «дно» потока горной массы.
Для защиты кромки окна и удержания слоя самофутеровки в конце разгонного канала устанавливается стальная концевая лопатка. Для повышения ее износостойкости применяют одну или несколько твёрдосплавных вставок. В качестве вставок чаще всего используют спеченный твердый сплав – композиционный материал на основе карбида вольфрама со связкой из кобальта. Наиболее распространенная марка – ВК-8 (92 массовых % карбида вольфрама и 8% кобальта).
В процессе работы горная масса постепенно вытесняет речной песок, уплотняется и образует сплошной сцементированный слой самофутеровки. Уплотнение самофутеровки и ее сцепление (адгезия) с металлом обычно столь велики, что ее удается отбить от ускорителя (при необходимости ремонта и замены футеровки) только с помощью молотка и зубила.
Описанная выше компоновка ускорителя «Barmac» стала прототипом ускорителя для современных центробежно-ударной дробилки, так как сочетает минимальный износ и удобство замены съемных деталей на демонтированном ускорителе.
Защита отражательной поверхности камеры дробления во многих центробежных дробилках также обеспечивается слоем самофутеровки. На периферии камеры дробления располагается горизонтальная кольцевая площадка, на которой сама же измельчаемая горная масса образует коническую поверхность с естественным углом откоса (рис 3).
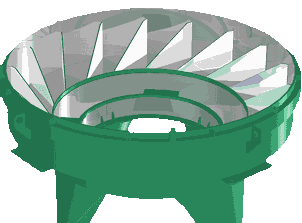
Рис. 3. Пример расположения косынок в камере дробления
Куски горной массы дробятся в основном на этой конической отражательной поверхности при соударении со слоем самофутеровки. Значительная часть осколков отражается от нее вверх. При их падении под действием силы тяжести они повторно соударяются с потоком из ускорителя. Но эффективность использования кинетической энергии кусков в дробилках «камень о камень» при прочих равных ниже, чем в дробилках «камень о металл».
Эффективность ударного взаимодействия снижается из-за того, что удар потока камней, вылетающих из ускорителя, приходится по касательной к кольцевой отбойной поверхности самофутеровки. Но острый угол, характеризующий соударение, увеличивается при увеличении зазора между ускорителем и отбойной поверхностью.
Испытания при переработке сталеплавильных и оловянных шлаков, хромовой и железной руды, гранитов, кварцитов, каолинов, известняков и фосфатов подтвердили высокую эффективность, экономичность и надежность дробилки «Бармак Ротопактор». Спрос на них увеличился, и в середине 80-х годов к производству центробежной дробилки приступили фирмы «Бармак Америка», США, и «Крофт Имприсэ», Великобритания. В настоящее время производится около 20 типоразмеров центробежных дробилок производительностью от 50 до 500 т/ч.
Современные производители центробежных дробилок
Широкое распространение и успех дробилки «Бармак Ротопактор» обеспечили популярность принципу центробежно-ударного дробления, который до этого не рассматривался в качестве серьезной альтернативы традиционным способам. Эти события заметно оживили рынок. Хотя дробилки «Бармак Ротопактор» реализуют принцип дробления «камень о камень», шире стали применяться и дробилки, дробящие «камень о металл». К производству и модернизации центробежно-ударной дробилки активно приступили фирмы, не занимавшиеся этой техникой прежде, а также те, которые ранее уже выпускали данную продукцию, в частности, конструкции типа «Tornado» или «Spokane».
Компания «Сидэррэпидс Айова», США, выпускает дробилки VSI с электрическим и дизельным приводом. Открытый ускоритель снабжен разгонными ребрами, выполненными из материала с высоким содержанием карбида хрома. Отражательная поверхность состоит из угловых отбойных плит, установленных на кольцевой обечайке. С целью снижения износа отбойных плит обечайка может быть повернута вокруг своей оси.
Kolberg Pioneer, США. Одна из крупнейших американских компаний, выпускающих дробилки центробежно-ударного типа. По конструкции достаточно близка фирме Barmac. Установки Kolberg Pioneer применяются при дроблении гранита, базальта и речного гравия и характеризуются низким абразивным износом вследствие реализации принципа дробления «камень о камень».
Компания Krupp , Германия, выпускает центробежно-ударные дробилки серии «Тайфун». Допустимая линейная скорость 60 м/с ускорителя диаметром 700–1100 мм.
Фирма SBM, Австрия, выпускает дробилки различных типоразмеров с ускорителем диаметром 800, 1000 и 1200 мм. Линейная скорость ускорителя составляет 60–74 м/с. Для защиты отражательной поверхности используется самофутеровка.
Несмотря на успехи американских и западноевропейских фирм на зарубежном рынке центробежно-ударных дробилок по-прежнему лидирует компания «Barmac», входящая в настоящее время в «Metco Minerals». Также одним из крупнейших производителей такого типа дробилки является Sandvic. Конструкция выпускаемых ими дробилки «Merlin» аналогична конструкции дробилки «Barmac».
Недостатки центробежной дробилки на подшипниковой опоре
Как уже было замечено, развитие техники ударного дробления-измельчения хрупких материалов сдерживает два основных противоречия: между необходимостью увеличения скорости соударения с целью повышения эффективности ударной дезинтеграции, с одной стороны, и снижением ресурса опорных подшипниковых узлов, а также ростом ударно-абразивного износа рабочих органов при увеличении скорости удара, с другой стороны.
Низкий ресурс и высокая чувствительность традиционных подшипниковых опорных узлов к ударным радиальным нагрузкам не позволяли увеличивать скорость удара куска руды о неподвижную преграду до требуемых при дезинтеграции руд значений, 70–100 м/с, если крупность максимальных кусков остается в пределах 40–70 мм. Таким образом, в случае использования подшипникового узла для достижения высокой производительности требуется сделать нелегкий выбор: либо крупность питания, либо скорость удара.
В результате, дробилки на подшипниковой опоре имеют ряд ограничений. Так, например, крупность исходного питания не должна превышать 50–60 мм (для абразивных материалов), диаметр ротора (ускорителя) должен быть не более 1 м, его линейная скорость ограничена 60–70 м/с для максимальных типоразмеров.
При данных ограничениях область применения ударной дезинтеграции ограничена в основном получением кубовидного щебня или искусственного песка, а измельчение руды до крупности ниже 5–10 мм становится неэффективным. Из-за малой скорости и, следовательно, низкого коэффициента измельчения высока степень возврата на додрабливание. Очевидно, что ударные дробилки, разработанные с применением традиционных подшипниковых узлов, пока не могут конкурировать с конусными дробилками мелкого дробления, стержневыми мельницами и мельницами полусамоизмельчения в существующих схемах рудоподготовки.
Воздушная опора – расширение возможностей центробежной дробилки
Для преодоления ограничений, накладываемых на скорость вращения ускорителей в дробилках на подшипниковых опорах, в конструкции центробежных дробилок была применена так называемая воздушная опора, первые упоминания (патенты) о которой можно встретить еще в начале ХХ века.
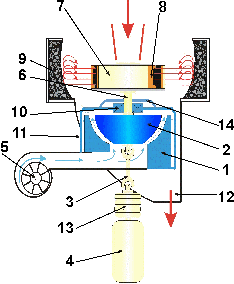
Рис. 4. Опорная часть центробежных дробилок на воздушной опоре
1 – Статор; 2 – ротор; 3 – карданный вал; 4 – электродвигатель;
5 – воздушный вентилятор; 6 – вал; 7 – ускоритель; 8 – концевая лопатка ускорителя;
9 – камера измельчения; 10 – предохранительный узел на случай аварийного отключения воздуха; 11 – крышка опорной части; 12 – патрубок для выгрузки дроблённого продукта;
13 – центробежная муфта; 14 – пыльник
Благодаря простой, но эффективной и надежной конструкции удалось решить ряд проблем, которые ранее считались неразрешимыми. Опора представляет собой две полусферы, в зазор между которыми нагнетается воздух. Требуется небольшое давление воздуха, достаточно типового напорного вентилятора. Роторная часть «всплывает» и выбирает ось вращения под действием внешних факторов. При этом значительно снижается чувствительность к дисбалансу (по сравнению с подшипниковыми аналогами – до 5–10 раз). Практически устраняются технические ограничения на размеры и скорость вращения роторных систем.
Концепция новой воздушной опоры доказала свою эффективность опытом практического применения в течение вот уже 15 лет и расширила диапазон линейных скоростей роторных систем при центробежной дезинтеграции до 100 м/с и более. В рамках этой концепции диаметры роторов, а вместе с ними и единичная производительность оборудования ограничены только техническими возможностями машиностроительных предприятий и условиями транспортировки.
Дальнейшее совершенствование техники ударной дезинтеграции связано с уменьшением ударно-абразивного износа рабочих органов. Роль износа возрастает с ростом скорости ускорителя, но уменьшается с ростом его диаметра. Это связано с тем, что одинаковая скорость на выходе достигается на большей длине, т.е. на большем роторе меньшее ускорение, а, следовательно, и меньше и износ за счет уменьшения прижимных сил. Научно-технические и машиностроительные работы продолжаются в обоих направлениях: по модернизации опорных узлов и снижению износа рабочих органов.
Перспективы развития ударной центробежной дезинтеграции
Очевидно, что в столь динамично развивающейся области техники, как ударная дезинтеграция, не может быть окончательных решений. Современное оборудование, реализующее способ центробежно-ударного дробления-измельчения, также является лишь очередным этапом в развитии техники ударной дезинтеграции твёрдых материалов.
В настоящее время можно уверенно говорить о том, что основной тенденцией развития техники дезинтеграции хрупких материалов является вытеснение новым, энергонапряженным оборудованием (в том числе ударного типа) традиционного оборудования, реализующего принципы раздавливания, истирания и низкоскоростного удара.
По мере того, как центробежно-ударные установки будут осваивать мелкое дробление (измельчение) руд, все более актуальными будут становиться среднее и грубое ударное дробление горных пород, переработка отходов, а также тонкое и сверхтонкое ударное измельчение полезных ископаемых и техногенного сырья, в том числе керамики, металлов, полимеров и смесей этих материалов.
Основные достоинства установок ударной центробежной дезинтеграции:
- Высокая степень сокращения крупности за счет высокой плотности вводимой мощности;
- Возможность организации как сухого, так и мокрого процесса дробления–измельчения;
- Стабильный гранулометрический состав продукта, так как он не зависит от износа рабочих органов;
- Простое управление гранулометрическим составом продукта путем изменения скорости вращения ротора;
- Низкая энергоемкость и металлоемкость, низкий уровень капитальных затрат, возможность организации процесса дезинтеграции под открытым небом;
- Удобный контроль износа рабочих органов и низкая трудоемкость технического обслуживания;
- Возможность селективного дробления и встроенной классификации