Ремонт после протечек (затопления) гипсокартона
Качественно выполненная облицовка стены или перегородка герметична, и поэтому в случае протечек или затопления следует перед началом ремонта гипсокартона спустить стоячую воду из полостей. Для этого при протечках (с потолка) или внизу (при затоплении) стен сначала шилом проколите контрольные отверстия, а затем ножом вырежьте отверстия для слива воды. При проведении этих работ следует соблюдать особую осторожность, так как пропитанная водой обшивка может обрушиться. Желательно также во избежание удара электрическим током обесточить коммуникации, проходящие в каркасном пространстве. Поврежденную тепло- и звукоизоляцию необходимо заменить.
Ремонт лицевого слоя гипсокартона
Картонная облицовка может быть повреждена при транспортировке, хранении, а также при несоблюдении технологии при производстве работ. В случае повреждения выполните следующие действия.
Установите дополнительные крепежные элементы около поврежденного участка, а только потом удалите старый крепеж. С помощью универсального ножа для резки гипсокартона обрежьте и удалите все неплотно прилегающие и (или) поврежденные части картона и гипса. Далее шпателем шириной 150 мм нанесите и разровняйте на поврежденном участке тонкий слой шпаклевки. Шпаклевка высохнет примерно через сутки. Затем слегка зачистите заделанную шпаклевкой поверхность шкуркой, при этом слишком усердствовать не надо, так как можно повредить лицевой картон при активной работе шкуркой или использовании слишком крупнозернистой шкурки. В случае необходимости можно нанести второй слой шпаклевки.
Заделка небольших отверстий в листах гипсокартона
Вырежьте из картона трафарет в виде квадрата или треугольника, имеющий размер, ненамного превышающий размер заделываемого отверстия в листе гипсокартона. Приложите трафарет к отверстию и обведите его карандашом или маркером. С помощью универсального ножа или универсальной пилы вырежьте в листе отверстие по обведенному контуру трафарета. Вырежьте из ненужного куска гипсокартона заплатку, имеющую размер, приблизительно на 50-60 мм превышающий размер трафарета.
Приложите трафарет к обратной стороне заплатки и обведите его карандашом.
Сделайте надрез на обратной стороне заплатки по обведенному контуру трафарета. Обломайте край заплатки по обведенному контуру, удалив лишние куски и оставив по всему краю заплатки лоскут лицевого картона шириной 50 мм. С помощью шпателя шириной приблизительно 100 мм нанесите тонкий слой шпаклевки вокруг отверстия на поверхность гипсокартона, внутрь отверстия и по краям заплатки-пробки. Вставьте пробку в отверстие и погрузите лоскут лицевого картона по краю заплатки в шпаклевку, нанесенную по краям отверстия. Убедитесь, что установленная заплатка находится вровень с поверхностью ремонтируемого листа гипсокартона. Разровняйте шпаклевку с помощью шпателя шириной 150 или 250 мм. Дайте шпаклевке застыть в течение 24 часов. Слегка зачистите заделанную шпаклевкой поверхность шкуркой или протрите ее влажной губкой для удаления пятен шпаклевки. Нанесите второй слой шпаклевки. Если необходимо, нанесите третий слой шпаклевки с помощью шпателя шириной 250 мм.
Вырежьте из картона трафарет в виде квадрата или треугольника, имеющий размер, ненамного превышающий размер заделываемого отверстия в листе гипсокартона. Приложите трафарет к отверстию и обведите его карандашом или маркером (рис. 1 а). С помощью универсального ножа или универсальной пилы вырежьте в листе гипсокартона отверстие по обведенному контуру трафарета. Вырежьте из фанеры несколько полосок для устройства обрешетки шириной около 25-75 мм, имеющих длину, приблизительно на 150 мм превышающую размер отверстия. Наложите полоски на отверстие и прикрепите их к обратной стороне гипсокартона с помощью нескольких шурупов (рис. 1 б). Вырежьте из ненужного куска гипсокартона заплатку, имеющую размер трафарета. Вставьте заплатку в отверстие и прикрепите ее к фанерным полоскам с помощью шурупов-саморезов (рис. 1 в).
Убедитесь в том, что установленная заплатка находится вровень с поверхностью ремонтируемого листа. С помощью шпателя шириной 100-150 мм нанесите тонкий слой шпаклевки вокруг отверстия на поверхности листа гипсокартона (рис. 1 г).
По стыку заплатки уложите армирующую ленту, вдавливая шпателем в слой шпаклевки. Нанесите тонкий накрывочный слой шпаклевки с помощью шпателя шириной 150 или 250 мм. Дайте шпаклевке застыть в течение 24 часов.
Слегка зачистите заделанную шпаклевкой поверхность шкуркой или протрите ее влажной губкой для удаления пятен шпаклевки (рис. 1 д). Нанесите второй и, если необходимо, третий слой шпаклевки аналогично с помощью шпателя шириной 250 мм (рис. 1 е).
Надрежьте крупные пузыри на ленте с помощью универсального ножа, а мелкие пузыри ликвидируйте, отрезая и удаляя образующую их ленту. Наполните пузырь на ленте шпаклевкой для заделки стыков. Погрузите участки ленты, образующие пузырь, в шпаклевку с помощью шпателя шириной 100 мм (рис. 2 а).
Разровняйте шпаклевку с помощью шпателя шириной 150 мм и дайте шпаклевке застыть в течение 24 часов. Слегка зачистите заделанную шпаклевкой поверхность шкуркой или протрите ее влажной губкой для удаления пятен шпаклевки. Нанесите второй слой шпаклевки при помощи шпателя шириной 150 или 250 мм (рис. 2 б).
С силой надавите на гипсокартон и вверните один шуруп на расстоянии 5 см от вылезшего шурупа. Вытащите вылезший шуруп и удалите всю отслоившуюся шпаклевку (рис. 3 а). С помощью шпателя шириной 100 мм заделайте каждую лунку, разравнивая шпаклевку, и дайте шпаклевке застыть в течение 24 часов. Слегка зачистите заделанную шпаклевкой поверхность шкуркой или протрите ее влажной губкой для удаления пятен шпаклевки. Нанесите второй слой шпаклевки с помощью шпателя шириной 150 мм и, при необходимости, третий слой с помощью шпателя шириной 250 мм (рис. 3 б).
С помощью шпателя шириной 100 мм нанесите тонкий слой шпаклевки на обе стороны угла. Перегните ленту для заделки стыков вдоль ее продольной оси симметрии (рис. 4 а). Наложите ленту для заделки стыков симметрично на угол и слегка вдавите ее в шпаклевку. Следует начать с одного конца трещины и двигаться к другому. Оторвите лишнюю часть ленты (рис. 4 б). С помощью шпателя внутренних углов погрузите ленту в шпаклевку. Держите шпатель под углом 45° к поверхности ленты и двигайте его, достаточно сильно прижимая к ленте, так чтобы из-под нее выступило некоторое количество шпаклевки. Начинайте от середины трещины и двигайтесь к ее краям.
Разровняйте шпаклевку с помощью шпателя для внутренних углов или шпателя шириной 150 мм и дайте шпаклевке застыть в течение 24 часов. Слегка зачистите заделанную шпаклевкой поверхность шкуркой или протрите ее влажной губкой для удаления пятен шпаклевки (рис. 4 г). Нанесите второй и третий слой шпаклевки. концам (рис. 4 в).
Очистив от шпаклевки отверстия угловой защитной накладки, укрепите ее планку шурупами с шагом не более 150 мм друг от друга по всей длине трещины (рис. 5 а,). С помощью шпателя шириной 100 мм нанесите тонкий слой шпаклевки на трещину (рис. 5 б). Разровняйте шпаклевку с помощью шпателя шириной 150 мм и дайте шпаклевке застыть в течение 24 часов. Слегка зачистите заделанную шпаклевкой поверхность шкуркой или протрите ее влажной губкой для удаления пятен шпаклевки. Нанесите второй слой шпаклевки.
Ремонт выступов на стыках листов гипсокартона
Зачистите выступающую часть стыка в целях как можно большего выравнивания ее с поверхностью листа гипсокартона, избегая при этом чрезмерных повреждении листа или нанесенной на стык ленты (рис. 6 а). С помощью шпателя шириной 250 мм нанесите тонкий слой шпаклевки на стык. Разровняйте шпаклевку на расстоянии примерно 250 мм от выступа по обеим его сторонам и дайте шпаклевке застыть в течение 24 часов (рис. 6 б). Слегка зачистите заделанную шпаклевкой поверхность шкуркой или протрите ее влажной губкой для удаления пятен шпаклевки. Нанесите второй и третий слои шпаклевки.
Ремонт трещин на ленте, наложенной на стыки
Удалите необходимое количество старой шпаклевки с поврежденного участка. С помощью шпателя шириной 100 мм нанесите тонкий слой шпаклевки вокруг поврежденного участка. Вдавите ленту для заделки стыков в шпаклевку с помощью шпателя шириной 100 мм (рис. 7 а). Разровняйте шпаклевку с помощью шпателя шириной 150 мм. Дайте шпаклевке застыть в течение 24 часов (рис. 7б). Слегка зачистите заделанную шпаклевкой поверхность шкуркой. Если необходимо, нанесите второй слой шпаклевки при помощи шпателя шириной 150 или 250 мм.
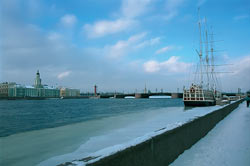
Последние десять лет развития строительной отрасли характеризуются значительным ростом капиталовложений в обновление основных средств производства. Во многом этому способствует наличие большого числа разнообразных лизинговых программ, возможность целевого кредитования и другие формы взаимодействия банков, поставщиков строительной техники и ее потенциальных покупателей. Сегодня на строительных площадках Санкт-Петербурга представлен широкий спектр оборудования для устройства свайных оснований. Мощные Junttan и проворные Casagrande, грандиозные Bauer и элегантные Woltman, великаны Fundex и малютки Klemm, стильные SoilMec и коренастые Atlas (а также Liebherr, EGT, KATO) – все они олицетворение того, что мы называем современными технологиями свайного фундаментостроения.
Отечественное буровое оборудование представлено машинами УРБ-2А2, УРБ-2М, УРБ-3АМ, ПБУ-50, ЛБУ, БГМ. СКБ, СБУ-100, УБС-СГ, БМ-811, БМ-831, СО-1200. На базе гидравлического экскаватора производятся буровые машины БМ-2001, БМ-3061.
Основываясь на практическом опыте работы, авторы статьи анализируют технологии и виды буронабивных и набивных свай, представленных на строительном рынке города, стараясь объективно изложить достоинства и недостатки каждой из известных технологий.
Чтобы лучше понять направления дальнейшего совершенствования технологий и способов геотехнического строительства в области фундаментостроения (и как его составной части – свайного фундаментостроения в сложных инженерно-геологических условиях Северо-Запада России), полезно оглянуться назад.
История свайного фундаментостроения, эволюция использования свай прошли через множество витков совершенствования технологий. А начиналось все с простых забивных деревянных свай.
Археологические раскопки на берегах Цюрихского озера показали, что сваи использовались человеком в глубокой древности – в эпоху неолита. Сначала они служили в качестве стоек, позволявших приподнять пол жилища над водой или землей. Римский архитектор и инженер Витрувий (I в. до н. э.) подчеркивал необходимость использования деревянных свай при строительстве на наносных или болотистых грунтах для передачи нагрузки от зданий на так называемый «материк». Позднее применение свай позволило возводить на слабых грунтах все более и более массивные сооружения.
Нельзя обойти вниманием опыт Нидерландов, где болотистая почва сделала сваи необходимой составляющей строительства. По свидетельству П. П. Гнедича только «благодаря сваям нидерландцы защитились от моря и отвоевали у него значительную площадь суши. Амстердам со своим населением в четверть миллиона человек весь стоит на сваях».
Петр I использовал опыт голландцев, о чем свидетельствует его письмо к И. Коробову, в котором он дает указание изучить «манер голландской архитектуры, а особливо фундаменты» из-за схожести грунтов. В 1715 году Петром издается приказ о подготовке к сентябрю, где есть следующая цитата «...каждый против своего дома паженные сваи для обивки берегов, мерою трехсаженные, числом сколько против каждого двора оных бы столбов могло пойти». И в ноябре этого же года – новый приказ «Об окончании Санкт-Петербургскими жителями к будущей весне бития свай против домов своих, по берегам большой и малой Невы и протокам, под опасением отобрания тех дворов». Согласно ему каждый житель обязан был бить сваи, закладывать за ними связки фашинника и утрамбовывать землю на берегу напротив своего участка.
![]() |
Рис. 1. Гаврила Скородумов. Строительство набережной Невы – фрагмент. |
Следы свайных построек мы находим и в архивных описаниях сердца Санкт-Петербурга – стрелки Васильевского острова. Зимой 1805 года началась реконструкция набережной стрелки по проекту генерал-лейтенанта Ф. И. Герарда. Из сметы на строительные работы видно, что на «построение намеченного берега противу биржи рустином в полуциркуль пошло: бревен на шпунтовые сваи длиной 3 х саженей шириной 8 вершков – 1500 шт.; круглых свай длиной 3 х саженей толщиной 6 вершков – 4025 шт.»
При капитальной реконструкции Дворцовой набережной в 1925 году обнаружилось, что вся ее проезжая часть опирается на сплошное свайное основание. О внешнем виде набережных (например, о том, что наклонные сваи закладывались деревянными щитами) можно судить по гравюрам А. Зубова и Х. Морселиуса.
Представляют интерес свидетельства современников строительства Исаакиевского собора, опубликованные в «Инженерном журнале» в 1861 году. «Работа фундамента произведена следующим образом: по отрытии фундаментной ямы, откачав из нея воду помощью Архимедовых винтов, которые работали постоянно и в последствии, в дно ямы всей ея поверхности были забиты частоколом сосновыя сваи от 11 до 12 д. в диаметре и длиною 3 саж. Расстояние между сваями равнялось диаметру их. Сваи были забиты до отказа бабою в 70 пуд. весом. Копров было 10; бабы на них поднимались помощью конных воротов, на каждом из которых работали 4 лошади. Работа эта продолжалась целый год и не прекращалась и зимою. Забивкою свай грунт был так уплотнен, что весьма трудно было отрывать его в промежутках между сваями. Срезка свай под одну горизонтальную плоскость была произведена очень просто: для этого действие водоотливных машин было приостановлено, и когда вода в фундаментной яме достигла желаемой высоты, то она тем самым отметила на каждой свае высоту, на которой ее нужно было срезать, что и было затем исполнено. Промежутки между головами свай были отрыты на 14 дюйм. и заполнены сильно утрамбованным древесным углем. После этой операции место постройки фундамента представляло совершенно горизонтальную плоскость. С забитыми в нее 10 762 сваями».
Долгое время забивка свай осуществлялась вручную. Первое описание примитивного ручного копра относится к 1660 году. Изобретение станины с направляющими для бабы и присоединение для ее подъема различных приспособлений позволило увеличить мощность снаряда. Несомненным достижением технической революции было изобретение Нэсмитом (Великобритания) паровой бабы. В 1889 году эта конструкция была усовершенствована русским инженером С. А. Арцишем, что позволило значительно увеличить ее производительность.
До 1838 года применялись только забивные сваи. Со временем они модернизировались – изменялся материал, при забивке свай в гравелистые и твердые грунты для деревянных свай стали использовать железные башмаки. В 1838 году Митчелл (Mitchall) предложил завинчивать сваи в грунт, для чего их нижняя часть снаряжалась винтом. Наконечники свай имели разный вид в зависимости от свойств грунта. В. Карлович в монографии «Основания и фундаменты» (1869 г.) признает преимущества винтовых свай перед забивными при применении их в некрепких грунтах, так как «концы их передают давление на большую площадь».
Так, почти два века назад было положено начало использованию буронабивных и винтовых свай.
Сегодня классификация свай по способу заглубления приводится в действующем Своде правил СП 50-102-2003 «Проектирование и устройство свайных фундаментов»:
- забивные (вдавливаемые) железобетонные, деревянные и стальные, погружаемые в грунт без его выемки или в лидерные скважины с помощью молотов, вибропогружателей, вибровдавливающих, виброударных и вдавливающих устройств;
- сваи-оболочки железобетонные, заглубляемые вибропогружателями с выемкой грунта и заполняемые частично или полностью бетонной смесью;
- набивные бетонные и железобетонные, устраиваемые в грунте путем укладки бетонной смеси в скважины, образованные в результате принудительного отжатия (вытеснения) грунта;
- буровые железобетонные, устраиваемые в грунте путем заполнения пробуренных скважин бетонной смесью или установки в них железобетонных элементов;
- винтовые;
- бурозавинчиваемые.
В свою очередь, набивные сваи по способу устройства подразделяются на:
- набивные, устраиваемые путем погружения инвентарных труб, нижний конец которых закрыт оставляемым в грунте башмаком или бетонной пробкой, с последующим извлечением этих труб по мере заполнения скважин бетонной смесью;
- набивные виброштампованные, устраиваемые в пробитых скважинах путем заполнения скважин жесткой бетонной смесью, уплотняемой виброштампом;
- набивные в выштампованном ложе, устраиваемые путем выштамповки в грунте скважин с последующим заполнением их бетонной смесью.
Буронабивные сваи по способу устройства подразделяются на:
- буронабивные сплошного сечения с уширениями и без них, бетонируемые в скважинах, пробуренных в глинистых грунтах выше уровня подземных вод без крепления стенок скважин, а в любых грунтах ниже уровня подземных вод – с закреплением стенок скважин глинистым раствором или инвентарными извлекаемыми обсадными трубами;
- буронабивные полые круглого сечения, устраиваемые с применением многосекционного вибросердечника;
- буронабивные сваи с уплотненным забоем, устраиваемые путем втрамбовывания в забой скважины щебня;
- буронабивные с камуфлетной пятой, устраиваемые путем бурения скважин с последующим образованием уширения взрывом и заполнением скважин бетонной смесью;
- буроинъекционные диаметром 0,15 – 0,25 м, устраиваемые в пробуренных скважинах путем нагнетания (инъекции) в них мелкозернистой бетонной смеси или цементно-песчаного раствора, или буроинъекционные с уплотнением окружающего грунта путем обработки скважин по разрядно-импульсной технологии;
- буроинъекционные, устраиваемые полым шнеком;
- сваи-столбы, устраиваемые путем бурения скважин с уширением или без него, укладки в них омоноличивающего цементно-песчаного раствора и опускания в скважины цилиндрических или призматических элементов сплошного сечения со сторонами или диаметром 0,8 м и более;
- буроопускные сваи с камуфлетной пятой.
Далеко не все из перечисленного применимо на строительных площадках Санкт-Петербурга. Ограничения связаны с особенными инженерно-геологическими условиями в черте города, которые характеризуются наличием большой толщи слабых пылевато-глинистых водонасыщенных грунтов, имеющих низкие прочностные свойства и обладающих тиксотропностью (то есть при динамических воздействиях переходящих в плывунное состояние).
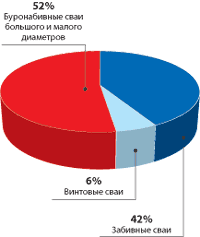
Рис. 2. Статистика использования разного вида свай (по Ван Импе).
В 2004 году Ван Импе, председатель международного комитета по фундаментостроению, представил следующую статистику использования разного вида свай в Европе:
- буронабивные сваи большого и малого диаметра занимают 52 % рынка;
- забивные сваи – 42 %;
- винтовые сваи – 6 %.
Почему именно буронабивным и набивным сваям большого и малого диаметра принадлежит пальма первенства? Ответ прост. Потому что только с их помощью удается решать сложный спектр конструктивных задач по устройству высокоэффективных свайных оснований. Только они делают возможным восприятие несущим слоем грунтов высоких (от 4000 до 25000 кН) нагрузок от высотных зданий и сооружений. Эти виды свай широко используются при строительстве внутри застроенных территорий, поскольку, являясь щадящими технологиями, исключают вибрационные и динамические воздействия на конструкции расположенных в непосредственной близости к строительной площадке существующих зданий. В практике международного строительства известны примеры устройства свай в районах с распространением слабых грунтов глубиной погружения до 75 м. В Санкт-Петербурге сваи с максимальной глубиной погружения 47,5 м были использованы при строительстве перехода на Ладожском вокзале.
Устройство буронабивных свай под защитой глинистого раствора
Выполняется станками вращательного бурения и включает в себя следующие операции:
- бурение скважины с использованием трехшарошечного долота;
- крепление стенок скважины глинистым (бентонитовым) раствором плотностью 1,15 – 1,3 г/см3, оказывающим гидростатическое давление на стенки скважины (при этом циркулирующий в скважине глинистый раствор выносит разрушенную породу на поверхность);
- бетонирование – выполняется подачей мелкозернистого бетона через буровой став (при диаметрах скважин до 350 мм) или через бетонолитную трубу, опускаемую до забоя скважины.
Бетонирование ведут методом вертикально перемещающейся трубы (ВПТ), т. е. постепенно поднимая бетонолитную трубу. Обязательным условием является постоянное нахождение нижнего конца трубы ниже уровня поверхности бетона в скважине не менее чем на 1 метр. Поступая в скважину, бетонная смесь вытесняет глинистый раствор.
|
В практике геотехнического строительства эта технология получила значительное распространение в связи с возможностью переоборудования под строительные цели отличающегося хорошей ремонтопригодностью и недорого (отсюда невысокие затраты на амортизацию) отечественного геологоразведочного бурового оборудования. Еще одним ее достоинством является отсутствие дополнительных осадок при ограниченном бурении скважин для устройства буронабивных свай в непосредственной близости от существующих зданий.
Диаметр свай при данном способе изготовления обычно находится в пределах 151 – 600 мм, но в практике мостостроения известны случаи бурения скважин диаметром до 1200 мм.
При использовании технологии бурения под защитой глинистого раствора, особое внимание следует обращать на соблюдение технологических параметров и качества производства работ. Так, в связи с высокой ценой бентонита (а она сопоставима со стоимостью цемента), в условиях Санкт-Петербурга используются местные каолиновые глинопорошки Никольского завода, что не позволяет многократно использовать этот раствор для промывки скважины без регенерации. При применении таких растворов для бурения скважин происходит их расслоение, а требуемая плотность, как правило, не обеспечивается без специальных добавок. При бурении с промывкой водой также необходимы специальные добавки (которые также весьма дороги) и постоянный строгий контроль их дозирования. Отмечается, что при бурении под глинистым раствором с использованием отечественного оборудования происходит отклонение скважины как по местоположению, так и по вертикали (особенно сильно это проявляется в техногенных грунтах и грунтах с плотными или валунными включениями). При устройстве свай большой длины (более 30 м) в процессе изготовления сваи возникает необходимость погружения армокаркаса в глинистый раствор, что сопровождается ослаблением сцепления арматуры с бетоном. Особого внимания в сваях, устраиваемых под защитой глинистого раствора, требует качество бетона (согласно СП при оценке прочности ствола сваи по материалу необходимо использовать дополнительные понижающие коэффициенты). Обычно в практике проектирования инженеры назначают нагрузку, передаваемую на устраиваемые по данной технологии сваи – не более 500 кН (для свай диаметром 350 мм).
На петербургском строительном рынке данную технологию используют специализированные фирмы: «Адепт», «Геострой», «Геоизол», «Циклон», «Основа», «СМУ 19 Метростроя», «Бек-Римас», «Промбурстрой», СК «Подземстройреконструкция», «Техпрогресс», «Старый город-Карст» и еще целый ряд других.
Технология устройства свай с короткими проходными шнеками
Получила свое развитие в начале 90 х годов прошлого столетия на базе использования российского парка бурильных машин: ПБУ, ЛБУ, БГМ, УБГ-СГ, СБУ-100. Сегодня кроме отечественных буровых установок в городе работают машины среднего класса западных фирм Klemm, Soilmec, Casagrande, EGT. Среди компаний, которые сегодня используют технологии коротких проходных шнеков, можно назвать «Адепт», «Геострой», «Циклон», «Основа», «Буровая компания», СК «Подземстройреконструкция», ЗАО «Техпрогресс», «Гидроспецстрой» и др.
|
При работе в стесненных условиях плотной городской застройки в последнее время хорошо зарекомендовали себя бурильные машины на базе малогабаритных буровых установок Klemm, Soilmec SM400, Casagrande C6, позволяющие устраивать буронабивные сваи диаметром до 450 мм и длиной до 25 – 30 м.
Технология ЗАО «Геострой» по устройству свай с использованием коротких проходных шнеков заключается в погружении шнеков на проектную глубину, нагнетании бетона по внутренней трубе шнека с помощью бетононасоса при одновременном его извлечении и последующем погружении армокаркаса при помощи вибропогружателя в заполненную бетоном скважину.
К преимуществам этой технологии относятся: отсутствие вибрации и ударов (что дает возможность работать вблизи существующих зданий), высокая несущая способность свай, высокая производительность (4 – 6 скважин глубиной 25 м в смену), хорошее качество заполнения скважины бетоном за счет подачи того под давлением, высокая точность постановки свай (весь процесс контролируется при помощи бортового компьютера). Данная технология оказывается вне всякой конкуренции на площадках с неравномерным напластованием грунтов.
Однако есть у нее особенности, требующие повышенного внимания. Так, требуется особо тщательное выполнение операции разъединения проходных шнеков при их подъеме, во избежание образования шеек и заплывания скважины грунтом. При бурении через прослои тугопластичных или полутвердых суглинков или глин скорость проходки снижается, поэтому необходим контроль соотношения скорости проходки и частоты вращения шнека для исключения выноса из скважины на дневную поверхность лишнего грунта. При бурении имеет место влияние на массив грунта, что вводит ограничение на количество одновременно устраиваемых скважин при работе вблизи существующих зданий (конкретно их число определяется ППР на основании геомониторинга).
Технология непрерывного проходного шнека
Или технология SOB-колонны, CFA, (от англ. continuous flight auger) впервые появилась в Санкт-Петербурге в 1997 году. Она использовалась французской фирмой «Солетанж Баши» при устройстве свай на строительстве Транспортно-коммерческого центра на Лиговском проспекте. Несмотря на предостережения геотехнической общественности, фирма не провела необходимых опытных работ и потерпела фиаско (были разрушены два здания). Кроме того, имело место нерасчетное поглощение бетона при подаче его в скважину. Так, при физическом объеме скважины – 7 м3, расход поглощения бетона последовательно выполненных свай составил – 16, 24, 38 и 56 м3. Данное обстоятельство заставило очень осторожно и технологически обоснованно внедрять технологию непрерывного проходного шнека на строительных площадках Санкт-Петербурга.
|
Наиболее безопасным для окружающих зданий оказалось бурение со сравнительно небольшой частотой вращения рабочего органа и как следствие – со значительным крутящим моментом (такой вид бурения принято называть медленновращательным). Оно производится разными по конструкции рабочими органами на основе шнекового бура.
Шнековый бур для медленновращательного бурения представляет собой механический бурильный инструмент, имеющий в качестве породоразрушающего элемента бурильную головку и шнек для аккумулирования и транспортировки на поверхность разрушенного грунта. Шнековые буры чаще всего изготавливают с одной (однозаходный), реже с двумя (двухзаходный) шнековыми спиралями. Торцы шнека, подверженные значительному износу, наплавляют износостойкими сплавами. Породоразрушающая бурильная головка имеет либо плоские, либо круглые резцы, а иногда комбинацию тех и других. Резцы снаряжены твердосплавными элементами, которые значительно повышают их износоустойчивость. В процессе эксплуатации, по мере износа они подлежат замене.
|
Применяемая ЗАО «Геострой» технология по устройству свай методом SOB-колонны заключается в погружении непрерывного проходного шнека на проектную глубину, извлечении грунта в объеме разбуриваемой скважины на поверхность, нагнетании бетона по внутренней трубе шнека при одновременном извлечении шнековой колонны и последующем погружении армокаркаса вибропогружателем в заполненную бетоном скважину. Таким образом, формирование сваи происходит без дополнительного крепления стенок скважины.
Технология незаменима для грунтов, имеющих слои, существенно отличающиеся по прочности. Особенно она эффективна при проходке большой толщи песков, полутвердых и тугопластичных суглинков, когда изготовление свай уплотнения невозможно.
Серьезным преимуществом является высокая производительность (до 79 свай глубиной 25 м в сутки) и высокое качество заполнения скважины бетоном, так как бетонная смесь подается под давлением при помощи бетононасоса.
Необходимо обратить внимание на то, что при устройстве свай по технологии SOB-колонны (CFA) происходит тиксотропное разупрочнение грунта в околосвайном массиве, следствием чего введено ограничение по ее использованию вблизи существующих зданий, если модуль деформации грунта меньше 5 МПа, а угол внутреннего трения меньше 10 градусов.
При устройстве буронабивных свай в водонасыщенных грунтах наиболее надежной защитой от обрушения стенок скважин при бурении является использование обсадных труб.
Технология устройства свай под защитой обсадной трубы
Наиболее распространенная в нашем регионе, она заключается в погружении инвентарной трубы с помощью вращателя и трубовкручивающего стола (осциллятора). В Санкт-Петербурге ее используют фирмы «МО 19», «Геострой», «Пилон», «Ленмостотрест», «Ризалит», ЗАО «СТиС», «Мостострой-6» и другие. Данная технология позволяет изготавливать буронабивные сваи диаметром 450, 600, 620, 700, 770, 880, 1000, 1200, 1500, 1800 мм. Известны примеры бурения скважин диаметром 1500 мм на глубину до 75 м. Наиболее глубокие в Санкт-Петербурге сваи (глубина бурения составила 47,5 м) были выполнены именно этим способом.
|
При строительстве Ладожского торгового центра свая диаметром 880 мм глубиной 26 м, испытанная нагрузкой 8640 кН, показала осадку всего 16 мм. При строительстве второй очереди Невского Паласа было проведено испытание сваи диаметром 880 мм глубиной погружения 32 мна нагрузку 6200 кН (осадка составила 12 мм) и диаметром 620 мм с глубиной погружения 32 м на нагрузку 4200 кН (осадка – около 20 мм). Это подтверждает возможности данных свай нести высокие нагрузки от зданий или сооружений.
Следует отметить, что при бурении в слабых водонасыщенных грунтах обсадная труба вкручивается с опережением относительно уровня выемки грунта (положения рабочего бурового органа). Таким образом формируется грунтовая пробка. Во избежание попадания грунта из-за трубного пространства внутрь скважины разницу хода между обсадной трубой и шнеком обычно принимают равной 3 – 4 м, иногда до 6 – 7 м (точно определяется ППР). В некоторых случаях при наличии напорных горизонтов подземных вод необходимо создание противодавленияв скважине посредством заполнения ее водой или глинистым раствором. Использование обсадной трубы позволяет перекрывать горизонты плывунных грунтов, обеспечивать безопасность ведения свайных работ, контролировать параметры буровой скважины, гарантировать высокое качество заполнения скважины бетоном. Данный вид свай является наиболее популярным среди транспортных строителей и мостостроителей в силу его высокой надежности.
Для выполнения буронабивных свай по технологии бурения скважины под защитой обсадной трубы используются буровые установки фирм Bauer ряда BG (в Санкт-Петербурге работают BG 7, BG 14, BG 25, BG 28, BG 30, BG 36), Casagrande (B 130, B250), Junttan (PM 25, PM 26, PM 30). Обсадная труба представляет собой секции труб, жестко соединенных между собой, толщина стенки обычно составляет 40 мм. Скорость проходки зависит от рабочих характеристик вращателя (прежде всего, мощности) и конструкции бурового органа (зависит от вида грунта).
Преимуществами данной технологии являются:
- Отсутствие динамических и вибрационных воздействий на грунт, что делает возможным устройство свай вблизи существующих зданий и сооружений.
- Высокая надежность современного оборудования позволяет безошибочно контролировать процесс бурения с достижением несущего слоя.
- Возможность разбуривания или извлечения валунов.
- Заполнение скважины производится через бетонолитную трубу, что исключает образование шеек при наличии в скважине арматурного каркаса.
- В процессе бурения осуществляется прямой контроль соответствия фактических инженерно-геологических условий проектным, что позволяет исключить ошибки и найти оптимальное решение.
- Возможность устройства уширения позволяет наиболее полно использовать несущую способность сваи.
При устройстве свай по данной технологии особое внимание необходимо обратить на то, что во время прохождения водонасыщенных грунтов, во избежание выпора грунта в скважине, необходимо создавать или грунтовую пробку большой длины, или избыточное давление с помощью воды или глинистого раствора. Принимая во внимание невысокую производительность и возможность воспринимать значительные нагрузки, проектные решения могут обеспечивать полное использование несущей способности свай по грунту. В качестве примера можно привести конструкцию использования системы «свая-колонна», что существенно минимизирует затраты на фундирование.
Для решения проблемы производительности инженерами фирмы Soilmec в сотрудничестве со специалистами ЗАО «Геострой» была разработана технология Double Rotary.
Технология двойного вращателя Double Rotary
Рис. 11. Технологическая карта устройства буронабивных свай методом Double Rotary.
Ее особенность – наличие системы двойного вращателя: верхний вращатель приводит в движение непрерывный проходной шнек, а нижний – поворачивает обсадную трубу в противоположном направлении. В Санкт-Петербурге для выполнения свай по данной технологии используются буровые машины фирм Soilmec CM120 и Bauer RTG-21. Возможны следующие размеры свай: 300, 350, 400, 450, 500, 550 мм. По окончании бурения по внутренней трубе проходного шнека из бетононасоса под давлением подается бетон. Технология двойного вращателя Double Rotary абсолютно безопасна при устройстве буронабивных свай вблизи существующих зданий.
К преимуществам устройства буронабивных свай методом Double Rotary можно отнести:
- Возможность ее применения для всех видов дисперсных грунтов (несвязные плотные грунты, илы, твердые глины).
- Отсутствие шума и значимых вибрационных воздействий позволяет устраивать сваи вблизи существующих зданий.
- Высокая производительность – до 24 свай глубиной до 25 м в смену.
- Высокое качество заполнения скважины бетоном за счет подачи бетона под давлением.
- Параметры бурения контролируются высокоточным бортовым компьютером.
- Возможность выполнять конструкции «стена в грунте» из секущихся свай.
Технология устройства набивных свай уплотнения (DDS)
Основана на принципе раскатки скважин, т. е. устраивается без выемки грунта, с уплотнением стенок скважины, посредством применения рабочего органа – раскатчика. Происходит непрерывный процесс образования цилиндрической полости в грунте путем его деформации и уплотнения раскатывающим механизмом в стенки скважины. Благодаря этому вокруг скважины образуется уплотненная зона грунта.
|
Раскатчик представляет собой ряд установленных последовательно друг на друга на общем валу конических катков, оси которых смещены относительно оси вала в стороны таким образом, что при вращении вала они катятся по винтовой линии, осуществляя подачу раскатчика. Это позволяет осуществлять проходку в грунте благодаря крутящему моменту, приложенному к валу раскатчика. Использование раскатчика обеспечивает бурение скважин с гладкими и прочными стенками значительного диаметра (до 1 м). И это с достаточно высокой скоростью, при отсутствии вибрации и шума, что делает технологию DDS особенно привлекательной при работе в условиях плотной городской застройки. Кроме того, ее применение снижает стоимость работ за счет экономии на затратах по вывозу грунта.
При реализации технологии устройства набивных свай уплотнения требуется жесткое соблюдение порядка ведения работ, так как и в других технологиях уплотнения возможно влияние на вблизи расположенные дома вследствие выпора грунта при массовом производстве работ (в случае, если процесс не регулируется ППР). К данному классу технологий относятся винтовые сваи. В Санкт-Петербурге они представлены оборудованием фирм Bauer, Fundex, Junttan и Atlas.
По сравнению с аналогичным оборудованием других производителей раскатчик фирмы BAUER позволяет гарантировать качество бетонирования за счет использования бетонолитной трубы, вмонтированной в буровой инструмент, а также повышение несущей способности свай благодаря опрессовке бетонной смеси в скважине. Использование специального бурового инструмента, жестко закрепленного на буровом ставе, делает возможным устройство свай через плотные слои песков, а при встрече с препятствиями (валуном, например) произвести замену породоразрушающего инструмента на забурник и продолжить бурение без потери сваи. Высокая точность постановки свай в плане, соблюдение вертикальности забуривания, глубина погружения рабочего органа, давление бетона при заполнении скважины – все это контролируется бортовым компьютером. Данная технология более 5 лет успешно применяется на строительных площадках нашего города. К ее достоинствам также следует отнести высокую производительность – до 30 свай глубиной до 25 м в смену.
Другая разновидность свай, изготавливаемых без выемки грунта, – сваи Atlas, разработчиком этой технологии является бельгийская Franki group. А в Санкт-Петербурге она эксклюзивно используется строительной компанией «Геоизол».
ATLAS COPCO
![]() |
Компания Atlas Copco справедливо считается одним из мировых лидеров во многих областях машиностроения, в т. ч. производстве бурового оборудования для горно-добывающей промышленности. Но только горным делом его применение не ограничивается. В большинстве европейских стран оно уже давно успешно применяется для инженерного бурения, в. т. ч. буровых работ в строительном комплексе. Круг задач, решаемых с помощью «строительного» бурового оборудования Atlas Copco, очень широк. Это и взрывные скважины, необходимые не только при проходке тоннелей, но и строительстве дорог и различных сооружений транспортного, энергетического и промышленного комплекса; бурение под анкерное крепление (например, для укрепления откосов при строительстве мостов), бурение при устройстве буронабивных свай. Последнее особенно актуально для тех крупных российских городов, чьи исторические центры активно реконструируются, где ведется новое строительство, в том числе и т. н. «уплотнительная» застройка. Здесь не обойтись без щадящих технологий, не допускающих даже намека на возможность повреждения находящихся в непосредственной близости от места работ конструкций. (Буронабивные сваи – это также единственный выход при строительстве на скальных грунтах). Кроме того, многие здания, построенные 100 и более лет назад, испытывающие прессинг резко возросших потоков транспорта и увеличившегося объема подземного строительства, нуждаются в работах по укреплению фундаментов. Производимые Atlas Copco небольшие буровые станки наилучшим образом подходят для этого. Они способны работать в самых стесненных условиях, некоторые модели способны даже проходить сквозь дверные проемы (это очень важно, поскольку зачастую скважины для укрепления фундаментов приходится бурить не только снаружи, но и изнутри зданий). Их немаловажное достоинство – низкие шум и вибрация.
Универсальные буровые установки Mustang используются в гидрогеологии, инженерной геологии, при устройстве фундаментов, для укрепления грунтов. С их помощью можно (при необходимости меняя буровое оборудование) реализовывать несколько видов бурения: шнековое, колонковое, погружным пневмоударником, вращательное (роторное шарошечными долотами), бурение OD, ODEX и DEPS. Сегодня производятся 4 модели: Mustang 4 (особенно хорошо подходит для бурения в ограниченном рабочем пространстве, имеет 4 модификации), Mustang 5 (буровая установка среднего размера; может быть легко оборудована специально спроектированными комплектами для струйной цементации колонн различной высоты; имеет 5 модификаций). Mustang 9 (установка повышенной мощности; для особо тяжелых условий эксплуатации; имеет 4 модификации), Mustang 13 (новейшая модель в семействе Mustang, разработанная для наиболее тяжелых условий эксплуатации; предусмотрено 3 модификации). Основное отличие «Мустангов» от конкурентов – повышенные момент вращения и подача.
Как строительные могут позиционироваться модели легкой серии с гидроперфоратором: ROC D3, ROC D5, ROC D7, ROC D9, ROC F7 и их модификации и исполнения (такие, как, например, с кабиной и без, с системой RRC, бесшумные, модификации с дистанционным управлением и т. д.) Всего производится 5 моделей и 10 исполнений. Полностью автоматизированные (автоматическая замена штанг обеспечивает очень высокую скорость бурения) они изначально изготавливаются под конкретное буровое оборудование – пневмоударник, гидроперфоратор и др.
В ассортименте компании есть также оборудование для нагнетания цементного раствора, используемое для стабилизации, уплотнения или укрепления грунта и скальных пород.
Преимущества бурового оборудования Atlas Copco – это не только надежность, экономичность и высокая производительность, но и высокая планка сервисного обслуживания, поддерживать которую помогает развитая сеть филиалов (основные – в Санкт-Петербурге, Екатеринбурге, Хабаровске, Мирном и плюс представительства во всех без исключения регионах), наличие складов в регионах (буровой инструмент, запасные части, расходные материалы), высокая квалификация специалистов.
Интерес представителей российского строительного комплекса к буровой технике Atlas Copco совпал с заинтересованностью компании в новых заказчиках. А значит, уже в самое ближайшее время эти машины можно будет увидеть на строительных площадках.
![]() |
Технология изготовления свай Atlas
Технологической особенностью свай Atlas (они относятся к набивным) является погружение обсадной трубы с оставляемым наконечником, что позволяет погружать бетонную смесь в сухой забой. Для устройства свай по данной технологии используются буровые машины BT-40, BT-60, обеспечивающие одновременное вращение и перемещение обсадной трубы. Данная технология предполагает наличие большого усилия для извлечения винтового наконечника. Технологический порядок выполнения работ при устройстве свай по данной технологии выглядит следующим образом:
- Ввинчивание трубы с винтовым режущим наконечником до проектной отметки.
- Установка армокаркаса в погруженную трубу и начало нагнетания бетонной смеси.
- Бетонирование с одновременным извлечением обсадной трубы, посредством вращения при помощи вертикальной тяги тросов (наконечник остается в грунте, что позволяет увеличивать несущую способность свай).
Применяются режущие наконечники диаметром: 360, 410, 460, 510 мм. По данным ООО «Геоизол» получаемый при их использовании диаметр винтовой поверхности составляет соответственно 530, 610, 670, 720 мм. Винтообразная поверхность формируется в тугопластичных и полутвердых глинистых грунтах; в мягкопластичных грунтах явно выраженной винтовой формы поверхности не образуется. Производительность – до 15 свай в смену.
![]() |
Рис. 14. Технология устройства свай Атлас. |
Технология изготовления набивных свай с использованием винтового теряемого наконечника включает в себя погружение инвентарной трубы, на нижнем конце которой закрепляется теряемый винтообразный наконечник. Различие заключается в форме теряемого наконечника и принципе формирования ствола сваи. Шаг винтовых лопастей и их форма определяются расчетом в зависимости от свойств разбуриваемого грунта. В Санкт-Петербурге применяются две различные технологии устройства данного вида свай – Fundex и Junttan. Обе основаны на одном принципе, хотя используются разные типы бурового оборудования. На строительном рынке данную технологию используют фирмы «Статика-Инжиниринг», «Старый город-Карст», «Геоизол», «БМГС».
![]() |
Рис. 15. Изготовление свай «Фундекс» на основе базовой машины F3500. |
Сваи Fundex изготавливаются установками вращательно-вдавливающего (извлекающего) действия (F12, F16, F 3500). Пятой будущей сваи служит «теряемый» чугунный винтовой наконечник, который выставляется на точку поверхности грунтового основания.
Сваи с теряемым наконечником Junttan выполняются с использованием универсальных базовых машин PM 25, PM 26 или PM 30, оснащенных вращателем с вращающим усилием 40 тxм.
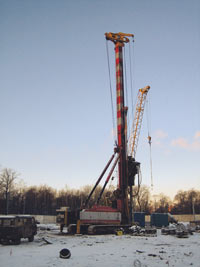
Рис. 16. Для выполнения работ используется буровая установка фирмы ЮнТан PМ-26.
К наконечнику с помощью специального соединения через тройную гидроизолирующую мягкую прокладку крепится нижний конец обсадной трубы, ее верхний конец зажимается в силовом рабочем органе бурового стола, перемещающегося по направляющей стреле.
Скважина для будущей сваи создается путем вращательно-вдавливающего погружения до заданной отметки системы «наконечник – буровая труба». В процессе бурения грунт раздвигается в радиальном направлении от оси скважины и одновременно уплотняется. По достижении наконечником проектной отметки труба проверяется на отсутствие воды.
В сухую инвентарную трубу через открытый верхний конец опускается арматурный каркас. Перед бетонной смесью для предотвращения ее расслоения в трубу подается порция праймера, состоящего из одной части цемента, одной части песка и одной части воды. После чего происходит порционное заполнение полости пластичным бетоном на мелком (5...20 мм) заполнителе с осадкой конуса 12...14 см посредством сбрасывания бетонной смеси из установленного на трубу бункера.
Извлечение буровой трубы из грунта производится возвратным вращением с одновременным вытягиванием.
Сваи Франки – буронабивные сваи, устраиваемые без выемки грунта, путем погружения инвентарных обсадных труб, нижний конец которых закрыт бетонной пробкой. Погружение трубы в грунт производится ударным способом до проектной отметки, далее трубу удерживают, предотвращая ее дальнейшее погружение, а пробку как бы вбивают в грунт, образуя тем самым уширение пяты сваи, диаметр которой в 1,5 – 2 раза превышает диаметр обсадной трубы.
Порядок выполнения работ:
- Установка обсадной трубы на точку бурения. Подача жесткой бетонной смеси в трубу и формирование пробки за счет ударов молота-трамбовки.
- Бетонная пробка схватывается с обсадной трубой и при последующих ударах молота начинает погружение в грунт, увлекая за собой трубу.
- После достижения проектной глубины обсадную трубу подвешивают на тросах и производят подачу жесткой железобетонной смеси. Ударами трамбовки выбивают пробку. Пробка втрамбовывается в грунт и образует уширенную пяту сваи.
- Затем в трубу погружают арматурный каркас и производят бетонирование с постепенным извлечением обсадной трубы.
В заключение необходимо подчеркнуть, что описанные выше технологии можно выполнять, используя оборудование разных фирм-производителей. При этом нельзя не отметить тенденцию универсализации базовых машин. В октябре 2006 года фирма SoilMec на дне открытых дверей назвала это явление многофункциональностью, придав ему статус «эволюции вида». Многофункциональность заключается в том, что краны и буровые установки могут быть использованы для сооружения свай и укрепления грунта по разным технологиям. Самой SoilMec начат выпуск новой продуктовой линейки – машин SR 20-110, с помощью которых, используя машину одной марки, можно реализовывать различные технологии: CFA, Double Rotary, Turbo Jet, Cutter Turbo Jet. Еще один пример – фирма Bauer, за три года до этого выпустившая новый ряд буровых машин RTG, позиционировавшихся именно как многофункциональные.
Начатый разговор о существующих и применяемых технологиях устройства буровых и буронабивных свай, на наш взгляд, необходимо продолжать более детальным обзором новых технологий, пока еще не представленных на строительных площадках нашего города.
Один из механизированных аналогов для резки дерева - это стационарный лобзиковый станок (рис. 1). Он также имеет ступенчатую регулировку оборотов. Для удобства пиления специально подается струя воздуха, которая очищает линию распила. Станок имеет мощную литую раму, которая обеспечивает оптимальную устойчивость конструкции и почти полное отсутствие вибраций. Естественно, что такой станок недешев и приобретать его следует, очевидно, тем, кто профессионально занимается изготовлением изделий из дерева.
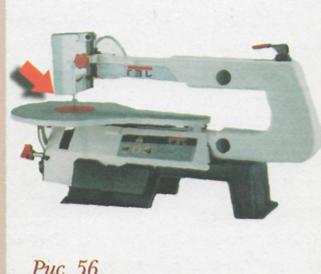
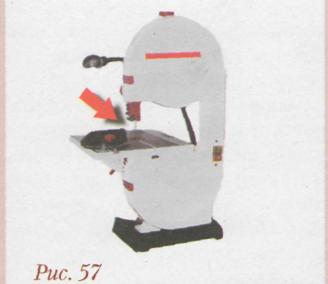
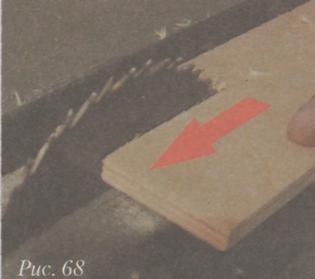
Рис. 4
При распиле делают несколько движений лезвием ножовки заранее нанесенной линии разметки, при этом лезвие направляют и заглубляют в древе. При дальнейшей работе необходимо корректировать движение ножовки, особенно в тех случаях , когда на линии распила встречается сучок. При пилении не нужно принять больших физических усилий. Все движения следует делать вразмах, то есть полностью использовать длину полотна ножовки.Для того чтобы было удобнее выполнять распиловку древесины очень важно установить вер стачную доску на оптимальную высоту. Для того чтобы точно определить высоту расположения верстачной доски, следует вплотную подойти к верстаку и опереться на него ладонями. Если при этом не приходится сгибать руки в локтях или наклоняться, чтобы достать до доски, высота выбрана правильно.
- древесина — 55 мм; - синтетические материалы — 25 мм; - мягкая сталь — 5 мм. Возможность косого пропила—до 45° в обе стороны. Масса пилы — 2,3 кг. Режим работы — продолжительный. Принцип работы ПЭМ относительно прост. Ножовочное полотно приводится в движение (возвратно-поступательное) штоком с помощью электродвигателя через понижающую зубчатую передачу и кулисный механизм (рис. 1).
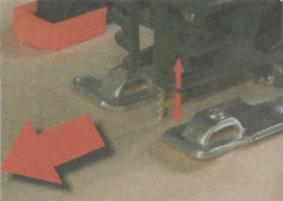
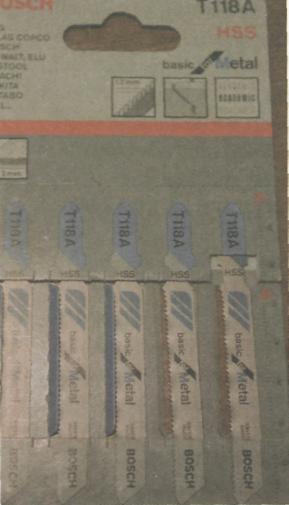
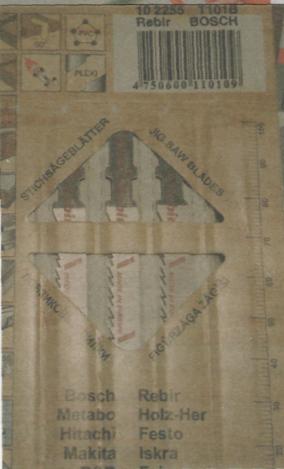
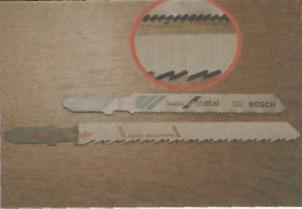
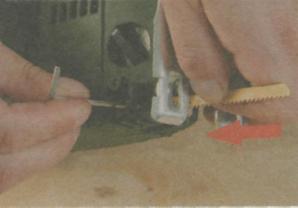
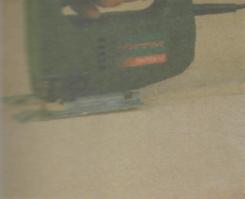
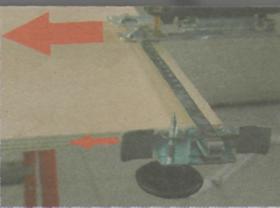
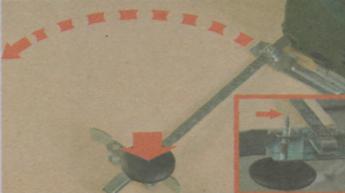
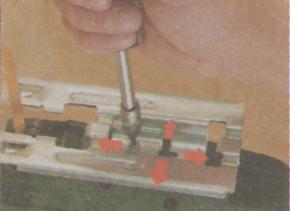
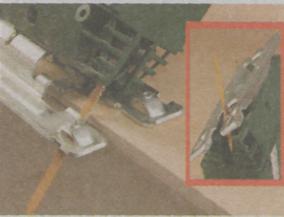
Удобство струнной пилки состоит в том, что при выпиливании сложных деталей ею легко осуществлять повороты практически на месте.
При соединении деревянных деталей практически невозможно обойтись без клея. Конечно, существуют различные виды крепежа, однако далеко не всегда удобно использовать гвозди и шурупы на видных местах изделий. Именно тогда на помощь приходит клей.
Прежде чем начать клеить, необходимо подготовить инструмент для фиксации склеиваемых деталей — струбцины. Их ассортимент весьма разнообразен. Наиболее прочные и надежные — металлические струбцины, однако, как правило, их щечки тоже из металла и при сильном сжатии могут повредить деревянные детали. Поэтому приходится подкладывать деревянные прокладки под щечки металлических струбцин. Гораздо удобнее струбцины из полимерных материалов. Они не повреждают заготовки, хотя выдерживают значительно меньшие гузки, чем струбцины из металла. Современные струбцины из полимерных материалов имеют специальные механизмы и приспособления для удобства и ускорения работы. Есть достаточно большие струбцины, способные сжать детали до 1 м и более. Несущий стержень у таких струбцин, как правило, металлический, а вот передвижные щечки — пластинные. Если перевернуть щечки такой струбцины наоборот, ее можно использовать не только сжатие, но и на распор. В больших струбцинах есть специальные механизмы, позволяющие сжимать заготовки одной рукой, лишь нажимая на специальный курок. Но вернемся к процессу склеивания. Все клеи можно разделить на природные и синтетические. В последние годы в связи с бурным развитием химии первые значительно уступили последним. Не имеет смысла рассказывать о классическом костном столярном клее, который сейчас почти не используется. Любой клей, который вам может потребоваться для работы, состоит из нескольких компонентов: собственно клеящего вещества, растворителя (он поддерживает определенную консистенцию состава), отвердителя и антисептиков. Наиболее известным и применяемым в быту клеем является клей ПВА (поливинилацетатная дисперсия). Этот клей достаточно быстро схватывается и поэтому потребует от вас определенных навыков и быстроты в работе. К «долгоиграющим» клеям относится универсальный эпоксидный клей, хотя скорость его застывания зависит напрямую от количества отвердителя, которое вы добавили в смолу. Наибольшее распространение в настоящее время получили универсальные клеи, которые иногда еще называют «жидкие гвозди» (рис. 1).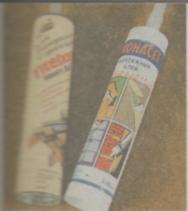
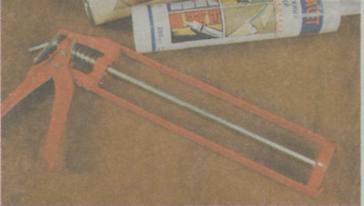
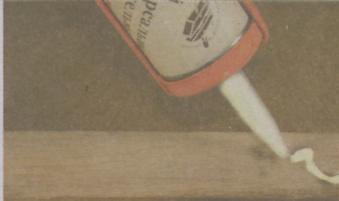
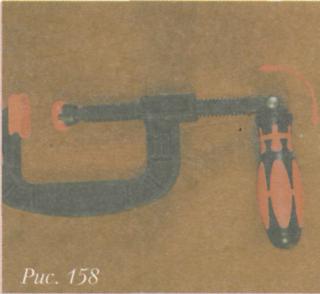
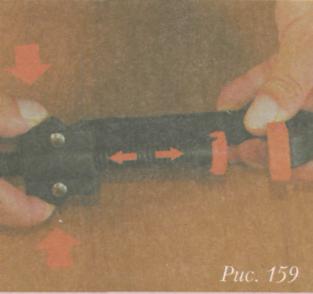
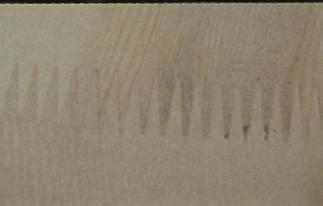
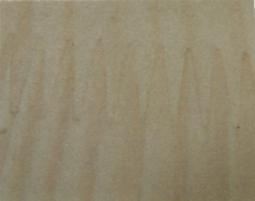
Рис. 9
Содержание статьи
Подготовка ванной комнаты
Укладка плитки на стену
Укладка плитки на пол ванной
Обработка межплиточных швов
Инструмент для укладки плитки
Клеевые составы для укладки
Перед укладкой плитки рекомендуется определиться с размером плитки. Если ванная комната узкая, а потолки высокие, лучше располагать плитку горизонтально, тогда помещение будет казаться шире, а потолки немного ниже. Подумайте о рисунке укладки. До потолка или до половины стены будет доходить плитка, сколько потребуется декоративных элементов (бордюров, вставок). Определите, чем закончится последний ряд. Красиво смотрятся бордюры «карандаш».
Следующий этап — подсчёт необходимого количества плитки для ванной комнаты. Для этого на листочке в клеточку нарисуйте план ванной комнаты, нанесите рисунок укладки и обозначьте место всех бордюров и декоров c точностью до одной штуки. По такому плану будет удобно подсчитывать нужное количество плитки. Покупать плитку лучше с запасом (как правило, это 15%).
Подготовка ванной комнаты
Прежде чем укладывать плитку в ванной, убедитесь, что стены ванной комнаты строго перпендикулярны друг другу, потолку и полу. Лучше всего это проверить с помощью уровня. Если существует малейшее отклонение, после укладки плитки кривизна будет сразу бросаться в глаза. Выравнивание поверхностей стен ванной комнаты — один из самых важных этапов укладки керамической плитки в ванной комнате. Чем качественнее выполнена подготовка поверхности под плитку, тем проще укладывать плитку на пол в ванной. Старую плитку на стенах и на полу необходимо сбить.
Для выравнивания стен ванной комнаты можно использовать влагостойкий гипсокартон, штукатурку или выравнивающие смеси. Работать с гипсокартоном проще и быстрее, но он «съест» несколько сантиметров площади. Для дополнительной прочности основания под плитку используйте два слоя гипсокартона.
Прежде чем штукатурить стены ванной комнаты, следует выставить «маяки» (выполненные по уровню вертикальные слои штукатурки) и, ориентируясь на них, оштукатурить все стены (рис. 1а, 1б, 1в).
Выравнивающие смеси используют, если кривизна поверхности стены минимальна. Перед укладкой плитки в ванной,стены и пол грунтуют. Грунтовка укрепляет основание, «убивает» пыль и обеспечивает лучшее сцепление плитки со стеной.
Поверхность можно не грунтовать, если плитка укладывается на клеевую смесь на крепкое основание (бетон, крепкая штукатурка). Грунтовка и клеевые составы должны соответствовать поверхностям, на которые наносятся, и типу помещения. Для ванных комнат советуем влагостойкие смеси.
Укладка плитки на стену
Укладку плитки в небольшом ванной многие мастера начинают со стены. Вначале разложите плитку на полу и посмотрите, какой получается рисунок. Регулярно повторяющаяся линия у плитки «под камень» может портить восприятие в целом. В этом случае попробуйте повернуть плитку (каждую, в шахматном порядке или каждую четвертую).
Необходимо точно знать расположение плиток на стене. Если ширина стены ванной является кратной ширине плитки (например, на стене помещается 10 рядов целой плитки), то плитка будет укладываться без подрезки. В этом случае в углу выкладывается первый вертикальный ряд, затем нижний горизонтальный ряд, а потом последовательно заполняется оставшееся пространство (рис. 2).
Если ширина плитки не кратна ширине стены, возможны два варианта проведения работ:
1. Выбирают «красный» угол и именно с него начинают выкладывать плитку. Подрезанная плитка таким образом оказывается в т. н. «невидимом» углу (рис. 3). Этот способ укладки плитки в ванной рекомендуется в случае, если «подрезанная» плитка равна не менее 1/2 целой плитки.
2. Если же подрезка получается меньше 1/2 целой плитки (3-5 см), то стену делят пополам и выкладывают плитку таким образом, чтобы центр стены ванной приходился на межплиточный шов или середину целой плитки, а подрезанная плитка поместилась бы по краям стены, имея при этом одинаковую ширину (рис. 4).
Как правило, в ванной комнате плитка укладывается от края ванны или от пола. В первом случае на уровне верхнего края ванны строго горизонтально по периметру всей ванной комнаты закрепляется рейка — основание для последующей укладки рядов вверх (рис. 5). Рейка убирается после высыхания раствора, когда плитки уже нельзя сдвинуть. Затем ряды отсчитываются вниз, и под начало первого ряда целой плитки снова прибивается рейка. От рейки плитка укладывается снизу вверх, заполняя оставшееся пространство. Рекомендуется наметить карандашом на стене несколько вертикальных линий, что позволит не допускать отклонения.
Если плитка укладывается от пола, то рейка прибивается под первый снизу ряд целой плитки (второй ряд от пола), и плитка укладывается вверх (рис. 6). Если все расчёты произведены правильно, то верхний край ванны должен совпадать с началом целого ряда плитки.
Первый цокольный ряд образуется из подрезанной плитки. Этот ряд рекомендуется выводить после укладки пола, чтобы скрыть неровные края напольных плиток, которые хуже подрезаются из-за большей твёрдости. Непосредственно от пола плитка укладывается только в том случае, если поверхность пола совершенно ровная по горизонтали.
Стена ванной, где находится дверь, облицовывается в последнюю очередь. Начинают с облицовки угла, противоположного «красному», затем выкладывают плиткой поверхность непосредственно над дверью (рис. 7). После этого на оставшейся поверхности проводят горизонтальные и вертикальные линии — графическое продолжение уже имеющихся межплиточных швов. Ориентируясь строго по этим линиям, завершают укладку плитки.
Швы на всех стенах должны совпадать, составляя единую линию. Чтобы получить ровные, одинаковые швы между плитками, рекомендуем применять дистанционные крестики (рис. 8).
Выступающий угол ванной облицовывается плиткой с помощью пластикового уголка или путём стачивания поверхностей соприкасающихся плиток под углом 45 градусов. Направление укладки — от выступающего угла к стенам (рис. 9).
Учитывая, что клеевой раствор сохраняет свои свойства, как правило, не дольше 30 минут (время зависит от типа основы, температуры и влажности воздуха в помещении и обозначается на упаковке клеевого состава), наносить его следует на поверхность, не превышающую одного квадратного метра. Раствор наносится гладкой стороной шпателя, затем равномерно распределяется зубчатой. Утративший свои свойства засохший раствор необходимо удалять и наносить новый.
Укладка плитки на пол ванной
Существует много вариантов рисунка укладки напольной плитки в ванной комнате. Самый простой и распространённый, который подходит для всех помещений, — параллельно стенам. Более сложный и менее экономичный (плитку приходится подрезать) — диагональная укладка, которая хорошо смотрится в просторных помещениях.
Большое значение имеют видимый угол и сторона, с которой мы заходим в помещение. У входа лучше укладывать целую плитку, подрезанная на пороге смотрится некрасиво. То же самое относится и к видимому углу помещения.
Вначале просто разложите плитку на полу ванной, чтобы знать, как поверхность будет выглядеть после укладки, и скорректировать возможные отклонения. Надёжнее начинать укладку плитки от порога вглубь, дойти до середины, остановиться и закончить на другой день. Это займёт больше времени, чем укладка от дальней стены по направлению к выходу, но гарантирует ровно уложенные ряды у порога ванной (рис. 10).
Выложив пол, подождите дня 3-4, пока раствор не высохнет. Первые сутки (или как минимум 12 часов) по плитке желательно вообще не ходить. Время полного высыхания зависит от типа раствора, толщины слоя и влажности помещения.
Обработка межплиточных швов
Минимум через сутки после укладки настенной плитки можно приступать к затирке швов, используя специальный раствор (затирку) нужного цвета. Сначала швы очищаются от остатков клеевого раствора, затем с помощью резинового шпателя заполняются затиркой. Спустя время, указанное на упаковке затирки, следует влажной губкой удалить излишки с поверхности. Когда раствор высохнет, можно приступать к окончательной очистке, используя мягкую ткань и жёсткую губку. Таким же образом производят затирку межплиточных швов в напольной плитке ванны. Но в данном случае не рекомендуем затирку белого цвета (рис. 11).
Для оформления стыков поверхностей (стены и ванной, стены и пола, стены и дверного косяка) лучше использовать материалы, которые обеспечивают герметичность швов, например, силиконовый санитарный герметик с антисептическими добавками против грибка. Герметик и затирки следует подбирать под цвет плитки (рис.12).
Стык ванны и стены можно оформить керамическим или пластиковым плинтусом или оставить небольшой шов в 2-3 мм.
Если вы закладываете ванну плиткой спереди, следует оставить окно для доступа к трубам. Оно закрывается плиткой, посаженной на магниты, а снаружи прикрепляется ручка. Швы замазывать не нужно. Не забудьте оставить небольшую нишу, куда бы заходили ступни ног, чтобы удобнее было наклоняться.
Если над раковиной вы решите расположить зеркало в раме из керамического бордюра, то сначала следует выложить настенную плитку вместе с бордюром, оставляя пространство необходимого размера под зеркало. Затем герметизируется поверхность стены, на край зеркала по всему периметру наносятся «жидкие гвозди» или другой клей, который не испортит амальгаму зеркала с тыльной стороны. Затем зеркало «вставляется» в раму из бордюра. Шов между зеркалом и бордюром герметизируется.
Инструмент для укладки плитки
Для укладки плитки потребуются плиткорез, уровень для определения кривизны поверхности, гладкий шпатель для предварительного выравнивания поверхности (рис.13), шпатель гребенчатый для нанесения раствора (рис.14), резиновый шпатель для нанесения замазки для швов. Для напольной и настенной плитки требуется гребенчатый шпатель с зубцами разной высоты: чем больше и тяжелее плитка, тем крупнее размер зубцов.
Станок для стачивания краев плитки под угол 45 градусов необходим, если требуется облицевать углы без применения пластикового уголка. Специальные насадки для дрели позволяют вырезать ровные отверстия в плитке, которая будет уложена в месте вывода труб и розеток.
Клеевые составы для укладки плитки
Современные производители предлагают специальные клеевые смеси в виде порошка, при добавлении воды в которые получается раствор, обладающий высокой фиксирующей способностью. В своей основе составы имеют цемент высокого качества и клеевую составляющую. В зависимости от последней составы различают по скорости, прочности схватывания и предназначению:
— для внутренней отделки стен на кухне и в санузле;
— для укладки напольной плитки;
— для внешней отделки цоколя и др.
Cуществуют по крайней мере три периода затвердевания клеевого состава:
— потеря подвижности соединений;
— готовность к началу эксплуатации;
— полное отвердение.
Первый этап — это время, в течение которого можно укладывать плитку или исправлять её положение. Поэтому целесообразнее использовать составы, которые долго не теряют клеящую способность. Готовность к эксплуатации (когда по поверхности пола, например, уже можно ходить) совпадает с моментом начала работ по затирке швов и для большинства составов соответствует 24 часам. Время полного отвердения наступает обычно через несколько суток.
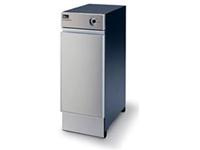
Одним из важных элементов оборудования любой кухни является контейнер для отходов. С некоторых пор место обычного мусорного ведра на многих кухнях заняло новое удобное устройство – пресс для мусора.
Прессы для бытовых отходов - это оборудование по сбору, уплотнению и транспортировке мусора. Это приспособление необычайно удобно для использования как в быту, так и в различных общественных заведениях, например, ресторанах, супермаркетах, гостиницах, аэропортах и т.д.
В основе действия этого аппарата лежит работа мощного поршневого цилиндра, который прессует мусор, опускаясь на него с огромной силой. Так, например, у пресса для мусора In-Sink-Erator 8251, прилагаемое усилие поршня равняется 2270 кг.
Прессы для отходов различаются по внешнему виду, размеру и техническим характеристикам. При выборе стоит обратить внимание на такие качества как небольшой, компактный размер, достаточно мощная сила сжатия, высокая скорость, бесшумность и надежность его работы. Все прессы для отходов просты как в использовании, так и в их обслуживании. Выбор типа устройства зависит также от наличия необходимой площади для установки, вида отходов, времени накопления.
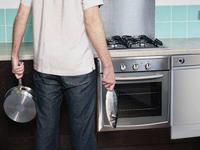
Преимущества использования прессов для мусора очевидны. В первую очередь это экологичность – закрытые, в некоторых случаях даже герметичные, накопители не просто не позволяют мусору высыпаться, а превращают отходы в сырье, которое в последствии может использоваться самым различным образом.
Еще один несомненный плюс – экономичность. Прессы для отходов позволяют снизить объем мусора более чем в 17 раз, что значительно сокращает транспортные расходы. Сокращение объема отходов к тому же обеспечивает рациональное использование территории и рабочего пространства.
Прессы для отходов, рассчитанные на использование в домашних условиях, устанавливаются в отделении шкафа под столешницей кухонной мебели. При этом его также можно установить в любом месте отдельно, достаточно лишь подключить его к сети.
Вместе с бытовым прессом обычно поставляются специальные пластиковые мешки для мусора, изготовленные из полиэтилена высокой плотности. При этом запрещается использовать обычные пластиковые мешки, так как они могут быть захвачены механизмом пресса и это вызовет неполадки.
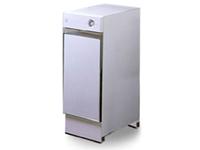
В заключение хочется сказать, что рост популярности такого вида оборудования как прессы для мусора позволил бы хотя бы частично решить проблему утилизации отходов, которая в настоящее время стоит достаточно остро. Уплотненные отходы принимаются переработчиками вторичного сырья, из них даже производят новые изделия. Так, например, в США отправляемый на свалку мусор перерабатывают в строительные материалы, например, для укладки автомобильных дорог. Хочется надеяться, что в ближайшем будущем пресс для мусора станет таким же обыденным предметом в наших домах, как холодильник.
![]() |
![]() |
Как найти стойки в гипсокартонной стене?
Гипсокартон не обладает достаточной прочностью, чтобы удерживать тяжелые шкафы и другую встроенную мебель. Шкафы должны поддерживаться каркасом строения, находящимся внутри стены. Это предполагает крепление мебели сквозь гипсокартон к степным стойкам. Центры стоек обычно стоят друг от друга на расстоянии 40,64 см. Если вы нашли одну стойку, то можете с помощью рулетки определить местонахождение других стоек.
Одним из самых простых и дешевых инструментов для обнаружения стоек является магнитный искатель. Эти приборы обнаруживают гвозди или шурупы, которыми прикреплены листы гиисокартона. Еще лучше, хотя дороже, электронный магнитный искатель, который можно купить в строительном супермаркете. Если магнитного искателя у вас нет, можно прозондировать стену небольшим гвоздем или тонким сверлом (если вы уверены, что установленный шкаф закроет проделанные отверстия).
Удаление гипсокартона
Некоторые проекты шкафов и мебели потребуют от вас удалить гипсокартон, чтобы встроить шкаф в стену. Планируя такой проект, убедитесь, что в той стене, куда вы хотите встроить шкаф, нет ни электрической проводки, ни канализационных труб. В противном случае вам придется перенести проводку или канализационные трубы на другое место. Даже если вы полагаете, что в стене, с которой вы собираетесь снимать гипсокартон, электрическая проводка отсутствует, все равно отключите электричество в этой части дома, чтобы гарантировать безопасность.
Ножовкой или пилой для гипсокартона прорежьте сухую штукатурку и удалите ее. Эта операция сопровождается обильной пылью, так что накройте близлежащие поверхности и не забудьте надеть пылезащитный респиратор или маску и защитные очки.
Удаление коврового покрытия. Если вы планируете установить шкаф и другую мебель на уже существующее покрытие пола – деревянное, кафельное или виниловое, смело ставьте его, удалять покрытие нет необходимости. Однако если на полу комнаты есть ковровое покрытие, перед установкой его следует снять. Перед тем как резать покрытие, измерьте основание шкафа (без молдинга!!!). Перенесите результаты своих измерений на то место, где будет установлен шкаф, и, пользуясь угольником и ножом, удалите ковровое покрытие и его подкладку.
Установка напольных шкафов
Не существует идеально горизонтальных полов или вертикальных стен. Поверхности даже самых лучших стен слегка волнисты; самые лучшие полы могут иметь едва заметный уклон. Эти небольшие несовершенства могут испортить самый совершенный проект.
![]() |
![]() |
К счастью, ко всем этим несовершенствам в ходе установки мебели и шкафов можно легко приспособиться.
Порядок установки шкафов и мебели такой:
1. Определите самую высокую точку пола. С помощью уровня определите самую высокую точку на том участке пола, на котором вы собираетесь установить шкаф или другую мебель. Чтобы это проделать, положите уровень на пол и проверьте горизонтальность пола. Если пол не горизонтален, перемещайте уровень вверх по наклону, до тех пор, пока воздушный пузырек не сдвинется в противоположную часть ампулы. Сделайте отметку на самой высокой точке пола.
2. Отметьте линию уровня. Сделайте отметку на стене на высоте, соответствующей расстоянию от самой высокой точки пола до верха шкафа. С помощью уровня проведите через эту отметку горизонтальную линию на стене на всю ширину вашего шкафа.
3. Установите шкаф. Придвиньте шкаф к стене и проверьте, совпадает ли его верх с линией уровня. Чтобы наклонить шкаф вперед, вставьте деревянные распорки между стеной и задней стенкой шкафа. С помощью других распорок выровняйте шкаф по горизонтали. Когда шкаф будет установлено по горизонтали и вертикали, прикрепите его к стойкам шурупами 9 см. Обрежьте распорки ножом заподлицо со шкафом.
![]() |
![]() |
4. Отделка защитных накладок. Существует по меньшей мере три способа закрыть щели, образовавшиеся в результате применения распорок. Для кухни или ванной, где полы влажные, простым и в то же время идеальным решением будет использование винилового молдинга. Такой молдинг можно просто приклеить. Он достаточно эластичен, чтобы его можно было прижать в нужных местах, а затем удалить излишек ножом. В сухих помещениях, например, в гостиной, где виниловый молдинг может выглядеть неуместным, вы можете облицевать защитную накладку полосой фанеры толщиной 6 мм.
Другой вариант – отделка полукруглым молдингом. Полукруглый молдинг будет выглядеть особенно уместным, если вы уже отделали им плинтусы в этом помещении.![]() |
![]() |
![]() |
Настенные шкафы устанавливать несколько труднее, чем напольные, поскольку их надо навешивать. Регулировка их положения может быть утомительным делом, если у вас нет подходящих опор. Классический способ избежать затруднений – временно прикрепить к стене брус, на который будет опираться нижний край шкафа. Во-первых, этот брус обеспечит горизонтальность, а во-вторых, вам больше не придется беспокоиться о своих уставших руках.
Порядок навешивания шкафов:
1. Установка бруса. С помощью уровня проведите на стене линию, обозначающую нижний край шкафа. Посредством 50 мм шурупов прикрепите временный брус по этой линии. Перед началом следующего этапа работы убедитесь, что шурупы попали в стойки и что брус расположен строго горизонтально.
2. Навешивание шкафа. Поставьте шкаф на брус и придвиньте его к стене как можно ближе. Вверните в верхнюю распорную поперечину шкафа два 76 мм шурупа, чтобы шкаф хорошо удерживался на стене. Проверьте с помощью уровня, висит ли шкаф вертикально. Возможно, вам придется подложить под заднюю стенку распорки. Укрепите на стене низ шкафа, ввернув в стойки два 76 мм шурупа сквозь нижнюю распорную поперечину.
3. Установка молдинга. Если на стене есть неровности или она не вертикальна, между стеной и шкафом могут быть щели. Их легко скрыть, установив вокруг шкафа полукруглый или другой уплотняющий молдинг.
Молдинг
Помимо украшения мебели, молдинг можно использовать для того, чтобы скрыть дыры от шурупов, гвоздей и других дефектов, неминуемо возникающих при работе. Чаще всего молдинг используют, когда необходимо скрыть щели между шкафом и стеной, шкафом и полом или двумя шкафами.
Удаление молдинга
Возможно, перед установкой встроенного шкафа вам потребуется удалить плинтус или карниз. Если сделать это аккуратно, позднее вы сможете вернуть его на прежнее место. Лучше всего начать удалять молдинг, пишет Инфобуд, с того места, где он начинается, – от двери или от угла. Если элементы молдинга на углу перекрываются, сначала удалите верхнюю часть, а потом нижнюю. Постепенно, начиная с конца, отделите молдинг от стены, действуя монтировкой как рычагом. Подводите монтировку как можно ближе к гвоздям и упирайте ее в деревянную щепку, чтобы не повредить стену.
После отделения части молдинга от стены переходите к следующему гвоздю. Продолжайте эту процедуру, до тех пор, пока нужная часть молдинга не будет удалена. Если молдинг не отделяется, с помощью добойника утопите гвозди. Гораздо легче потом замаскировать отверстия от гвоздей, чем восстановить сломанный молдинг.
Восстановление молдинга
Верните на свои места весь снятый ранее молдинг и добавьте новый, если это требуется. По возможности пользуйтесь уже имеющимися отверстиями для гвоздей. Вытаскивание гвоздей расширит отверстия, поэтому при восстановлении используйте более толстые гвозди.
Зашпаклюйте отверстия для гвоздей и окончательно отделайте свою работу. При восстановлении молдинга вам потребуется состыковать его на углах. Для внешних углов правильным решением будет соединение в ус. Для внутренних углов лучше использовать рельефное соединение. Правильно выполненные рельефные соединений выглядят безшовными, давая профилю плавно обтекать углы. Рельефные соединения более надежны, чем внутренние соединения в ус.
Рельефные соединения
1. Соедините молдинг под углом 45°, чтобы сделать рельефное соединение. Сначала скосите кусок молдинга так, как если бы вы устанавливали внутренний молдинг. Отметьте карандашом угол 90 градусов на верхней кромке молдинга. Затем карандашом проведите линию вдоль профиля молдинга, соответствующую косому срезу.
2. Обработка стыка молдинга. Перекройте шов подрезной пилой обрежьте молдинг по линии, где скос пересекается с лицевой частью молдинга. В тех случаях, когда молдинг обладает широкой плоской частью (как, к примеру, плинтус), вы можете воспользоваться станком для отрезания под углом, а затем обработать линию среза стамеской или напильником.
3. Завершение рельефного соединения. Установите перекрытый шов в позицию стыка, приложив молдинг к уже существующему образцу. Расположите свободный конец вдоль образца. На тыльной части молдинга поставьте отметку нужной длины и сделайте в этом месте прямой отрез.
Нарезка и установка карнизов
Независимо оттого, украшаете ли вы свой проект новым молдингом или же заново подрезаете и восстанавливаете молдинг, снятый при установке шкафа, вам будет несложно подрезать его с помощью электропилы для резания под углом или ножовки и стусла. Однако существует такой тип молдинга, пишет Инфобуд, который может представлять проблему – карниз. Из-за особого дизайна карниз иначе устанавливают и иначе режут.
Карниз идет под углом 45° к вертикальной поверхности, на которую его устанавливают. Это может быть место стыка стены с потолком или верх шкафа. Хитрость при резании и установке карниза состоит в том, чтобы установить его в стусле под тем же самым углом. Легче всего это проделать, перевернув карниз верхней стороной вниз, когда он находится в стусле или в зажиме электропилы для резания под углом.
Чтобы зафиксировать карниз, когда вы располагаете его под углом, прикрепите к направляющей планке ограничитель. Ограничитель представляет собой рейку квадратного сечения –19х19 мм, прикрепленную зажимом или шурупами.
Установка карниза
Укрепить карниз на стене несложно. Поместите его на стык стены с потолком и прибейте гвоздями. Если вы украшаете карнизом верх шкафа, установите его точно таким же образом. Возможно, вам потребуется прикрепить к верху шкафа скошенный брусок, чтобы обеспечить дополнительную опору для широкого карниза.
При установке карниза нет ничего хуже, чем валяющаяся в мастерской доска с торчащими из нее гвоздями. Вынимайте гвозди из плинтуса или карниза сразу же после демонтажа. Лучший способ удалить финишные гвозди из плинтуса и не повредить при этом его лицевую поверхность – это прогнать гвоздь насквозь и вытащить его с обратной стороны. Плоскогубцами или клещами ухватите острие гвоздя и вытащите его наружу, раскачивая инструмент из стороны в сторону. Если плинтус поврежден или же если вы не собираетесь использовать его повторно, загните выступающие гвозди молотком.
Навесные вентилируемые фасады (НВФ) обладают множеством преимуществ. Но их легко можно свести на нет, если нарушить технологию монтажа или неправильно подобрать материалы. В этой статье мы разберём основные ошибки монтажа навесных вентилируемых фасадов при строительстве или реконструкции различных объектов.
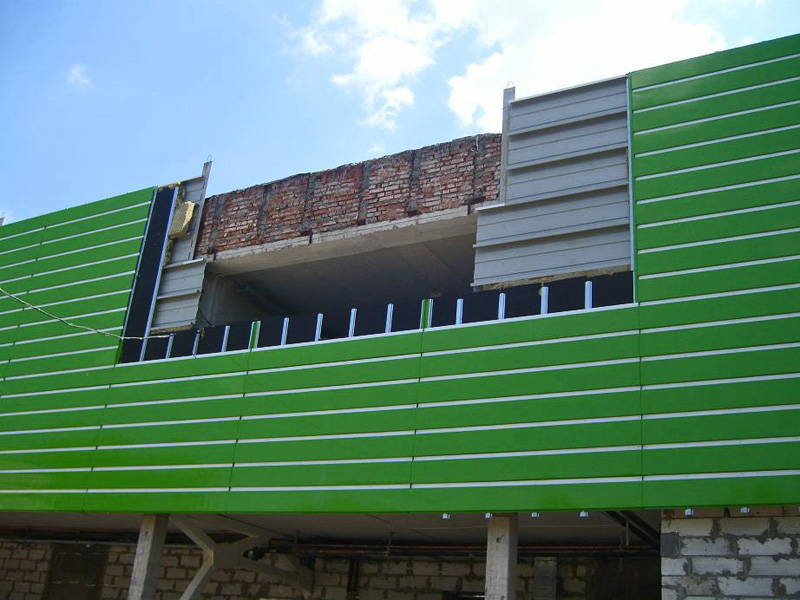
Чаще всего проблемы соблюдения технологии монтажа НВФ возникают в сегменте частного малоэтажного домостроения. Стремясь сэкономить, многие домовладельцы пользуются услугами непрофессиональных строителей, не представляющих, как обращаться с современными материалами. В результате уже через несколько лет фасад теряет свой привлекательный внешний вид и начинает разрушаться. К сожалению, подобные ситуации не редкость и в масштабном строительстве.
Вентилируемый фасад – это сложная инженерная система, каждый из компонентов которой решает свою задачу. Облицовочный материал защищает систему от внешнего воздействия и придаёт ей привлекательный вид; теплоизоляция, монтируемая на стену, улучшает теплотехнические и звукоизоляционные характеристики ограждающей конструкции; гидроветрозащитная мембрана обеспечивает защиту теплоизоляции от намокания, а вентиляционный зазор - эффективное удаление конденсата с обратной стороны облицовки, подконструкция распределяет нагрузку от фасадной системы по поверхности несущей стены. Очевидно, что неправильный подбор любого из перечисленных компонентов, использование несочетаемых материалов (материалов с противоречащими друг другу свойствами) или ошибки монтажа могут привести к нарушению функционирования всей системы.
Подконструкция и её размещение на несущей стене
Надёжность и долговечность фасада в первую очередь определяются даже не типом применяемых облицовочных материалов, а качеством изготовления и соблюдением технологии монтажа подконструкции.
Наиболее распространённая ошибка – попытки заменить рекомендованные производителем фасада кронштейны на более дешёвые и отличающиеся по своим характеристикам альтернативные варианты. Не предназначенные для НВФ кронштейны либо не обладают необходимой несущей способностью при всём диапазоне внешних условий, либо дополнительно ещё и нарушают свойства фасада, увеличивая площадь сечения так называемых «мостиков холода», снижая эффективность удаления водяных паров из толщи теплоизоляции и т.п.
Комментарий специалиста«Вентиляционный зазор навесного фасада определяется длиной устанавливаемого кронштейна. Поэтому когда строители пытаются экономить на кронштейнах, выбирая, к примеру, более короткие варианты или вообще используя произвольные товары-заменители со строительного рынка (вплоть до направляющих для гипсокартонного профиля или деревянные бруски), заказчик получает не вентилируемый фасад, а непроветриваемую конструкцию в результате чего теплоизоляция и несущие стены будут отсыревать и постепенно разрушаться. Внимание подконструкции следует уделять ещё и потому, что, например, тот же гипсокартонный профиль попросту не выдерживает проектных нагрузок. Возможно, такой фасад и не обвалится сразу. Но поскольку направляющие для гипсокартона, как правило, делают из обычной тонкой оцинковки без дополнительных защитных покрытий, на фасаде они очень быстро ржавеют и теряют несущую способность. Такой фасад довольно быстро потеряет свою геометрию, а его обрушение будет лишь вопросом времени», – рассказывает Ирина Зорькина, начальник отдела технического сопровождения продаж департамента фасадных систем и ограждающих конструкций Группы компаний Металл Профиль, крупнейшего российского производителя фасадных и кровельных систем.
Также специалист отмечает, что часто используемая вместо стальной, алюминиевая подконструкция может оказаться небезопасной при пожаре, поскольку температура в подфасадном пространстве может превышать температуру плавления алюминия. Особенно это опасно в случае использования не соответствующих требованиям пожарной безопасности композитных облицовок. Подобный подход недопустим при проектировании и строительстве современных зданий. На сегодняшний день наиболее надёжными в эксплуатации и безопасными являются стальная подконструкция с порошковой окраской.
Ещё одна распространённая ошибка – неправильная установка анкеров для кронштейнов в несущей стене. Если для бурения отверстий в бетонной плите можно использовать перфоратор, то в кирпичной кладке необходимо делать это исключительно с помощью дрели, соблюдая при этом требования по расположению отверстий относительно края стены и швов кладки. Несоблюдение этих условий ведёт к тому, что кронштейн не будет выдерживать заявленной нагрузки. Если подобных ошибок окажется много, результатом вполне может стать обрушение фасада. При монтаже НВФ на стенах из нестандартных материалов или сложной конфигурации специалисты советуют проводить испытания на вырыв крепёжных элементов.
Менее распространённая, но грозящая не меньшими негативными последствиями ошибка – отказ от использования прокладок при монтаже кронштейнов. В результате прямого контакта, например, с поверхностью бетонной стены, кронштейны быстро корродируют, что тоже в итоге сказывается на долговечности фасада.
Стоит отметить, что внимание к деталям при монтаже несущей конструкции, в конечном счете, отражается и на внешнем виде навесного фасада. Так, при использовании короткого уровня вместо отвеса фасад может потерять свою геометрию, что будет особенно заметно на больших площадях. Естественно, результат в этом случае вряд ли удовлетворит заказчика.
Утеплитель и его гидроизоляция
В современных вентилируемых фасадах чаще всего применяется негорючая и долговечная минеральная вата на основе базальтового волокна. Правда, порой на этапе проектирования её пытаются заменить на более дешёвые аналоги. Альтернатив в данном случае две: пенополистирол и минеральная вата на основе стекловолокна. И каждое из этих решений обладает своими особенностями.
Пенополистирол – весьма пожароопасный материал, который к тому же обладает низкой паропроницаемостью, что может повлечь за собой отсыревание ограждающих конструкций. Минеральная вата на основе стекловолокна с этой точки зрения обладает более универсальными эксплуатационными характеристиками, так что её использование нельзя однозначно рассматривать как ошибку. Основное преимущество базальтовой ваты ее лучшая огнестойкость по сравнению со стекловатой.
Для гидроизоляции, причём не только при использовании минеральной ваты на основе стекловолокна, рекомендуется применять гидроветрозащитные мембраны. И вот здесь у неопытных проектировщиков и монтажников часто возникают сложности.
Во-первых, из-за особенностей представленных ранее на рынке материалов существует стереотип об опасности мембран во время пожара. Как отмечают специалисты Du Pont, это уже давно не соответствует действительности, по крайней мере, в отношении мембран Tyvek. Таким образом, применение плёнок в качестве «безопасной альтернативы» уже давно не оправдано.
Во-вторых, при монтаже мембраны поверх утеплителя свою роль играет время. Если между распаковкой утеплителя и установкой мембраны проходит большое количество времени (недели или даже месяцы), минеральная вата на основе базальтового волокна наберёт в себя слишком много влаги. Чтобы этого не происходило, рекомендуется монтировать утеплитель и мембрану последовательно – так, чтобы утеплитель находился без защиты мембраны не более нескольких дней.
Ещё одна возможная ошибка – применение при укладке утеплителя не предназначенных для этого прокладок и уплотнителей. «Порой вместо предусмотренных проектом прокладок используются деревянные бруски или какие-то подобные решения. Монтажники просто не понимают, что, используя такие «уплотнители», они тем самым создают на фасаде мостик холода, существенно снижая его теплоизоляционные свойства. Кроме того, древесина намокает и со временем разрушается, так что о долговечности такого фасада говорить тоже не приходится. Для удобства, а также во избежание использования несоответствующих прокладок, ГК Металл Профиль комплектует всю линейку своих кронштейнов необходимыми прокладками», – объясняет Ирина Зорькина (ГК Металл Профиль).
Облицовочные материалы
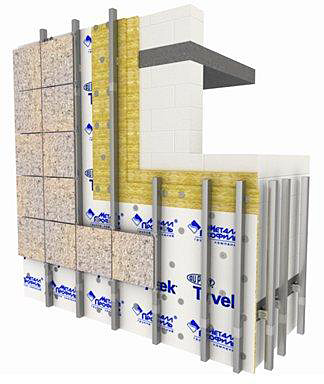
Навесные вентилируемые фасады предполагают широкий выбор облицовочных материалов. Но, как это обычно и бывает, универсального решения здесь не существует. Каждый материал обладает своими особенностями, ориентирован на свой сегмент и, естественно, тянет за собой свои собственные ошибки.
С каждым годом всё большей популярностью пользуются облицовки НВФ из стали с полимерным покрытием – линеарные панели, фасадные кассеты и стальной сайдинг. Залогом их успеха являются как эстетическая привлекательность и разнообразие оттеночных решений, так и длительный срок службы. Например, на фасадные облицовки из стали с покрытием Colorcoat Prisma производитель даёт 25 лет гарантии. При этом стальные материалы характеризуются существенно меньшим весом и куда более надёжным и безопасным способом крепления на фасаде по сравнению с распространённым керамогранитом.
Наиболее распространённая ошибка при работе со сталью с полимерным покрытием в любых вариациях – нарезка при помощи абразивного круга. «Подобные материалы нельзя резать «болгаркой». При такой раскройке металл нагревается, а это значит, что на достаточно большой площади вокруг шва выгорает не только полимерный слой, но и оцинковка. В итоге кромка достаточно быстро будет корродировать, что не только испортит внешний вид фасада, но и скажется на его долговечности», – поясняет Ирина Зорькина (ГК Металл Профиль).
К наименее проблемным, хоть и более заметным для заказчика ошибкам монтажа следует отнести нарушение геометрически правильного внешнего вида фасада. К примеру, невнимание к направлению отражения света при монтаже облицовки. Иногда монтажники не следят за тем, в каком направлении укладываются фасадные кассеты с глянцевой поверхностью. В результате зрительно цвет фасада на соседних участках отличается, поскольку они по-разному отражают солнечный свет. На фасадах большой площади подобные ошибки особенно заметны.
В заключение стоит отметить, что поскольку на монтаж навесных фасадов отсутствуют какие-либо ГОСТы и СНИПы, то за уровнем качества выполняемых работ всегда приходится следить их заказчику. Таким образом, гарантию того, что технология не нарушена, может дать лишь обращение к профессионалам, уже успевшим зарекомендовать себя на рынке. А поскольку характеристики фасада на практике зависят ещё и от сочетания используемых материалов, лучшей рекомендацией будет заказ фасадной системы у одного поставщика, отвечающего за качество всего комплекса.
Понимание свойств и особенностей эксплуатации вентилируемых фасадов позволяет избежать большинства проблем, обеспечив привлекательность внешнего вида фасада и сохранение его защитных свойств на протяжении всего срока эксплуатации.
Керамический кирпич имеет несколько разновидностей: строительный (он же рядовой, «обычный», «полнотелый»), пустотелый (он же «экономичный», «дырочный», «щелевой», «самонесущий»), облицовочный (лицевой), имееющий массу подвидов: фасадный, фасонный, фигурный, глазурованный, ангобированный. Виды кирпича могут сочетаться. Например, фасадный кирпич бывает и пустотелым, и полнотелым, а фасонный – и строительным, и облицовочным. По фактуре поверхности ложковой и тычковой граней изделия могут быть гладкими или рифлеными. Керамический материал используют также при кладке печей и каминов. Для тех частей, что непосредственно контактируют с открытым огнем, необходим шамотный (огнеупорный) кирпич, а для отделки берут «каминный» – аналог облицовочного фасонного. Клинкерным кирпичом мостят дорожки. Существует два метода изготовления керамического кирпича: пластический и полусухого прессования. В первом случае глиняную массу влажностью 17..30% выдавливают из ленточного пресса, затем сушат и обжигают. Второй способ менее распространен - сырец формируют из глины влажностью 8..10% сильным прессованием; такой материал не рекомендуют для строительства помещений с расчётной высокой влажностью. Нормативные требования к керамическому кирпичу В настоящее время действуют стандарты ГОСТ 7484-78 «Кирпич и камни керамические лицевые. Технические условия» и ГОСТ 530-95 «Кирпич и камни керамические. Технические условия», пришедший на смену ГОСТ 6316-74 и ГОСТ 648-73. Отсутствие брака означает:
Требования к внешнему виду облицовочного кирпича более строги: на лицевой наповерхности кирпича не должно быть сколов (в т. ч. и и от известковых включений), пятен, выцветов и других внешних дефектов, видимых с расстояния 10 м на открытом пространстве при дневном освещении. Браком являются случаи нарушения режима обжига кирпича. Признаки «недожога» – горчичный цвет, глухой звук при ударе. Результат такого брака – плохая водо- и морозостойкость. Для «пережога» характерны черные подпалины и оплывшая, нарушенная форма, повышенные плотность и теплопроводность (тепло из помещений будет «утекать» гораздо интенсивнее). Характеристики отдельных видов кирпича Табл. 1. Основные характеристики керамического кирпича |
Наименование | Средняя плотность, кг/м3 | Пористость, % | Марка морозостойкости | Коэфф. теплопроводности, Вт/м·°С | Марка прочности | Цвет | |
Кирпич полнотелый | 1600..1900 | 8 | 15..50 | 0,6..0,7 | 75..300 | красный | |
Кирпич пустотелый | 1000..1450 | 6..8 | 15..50 | 0,3..0,5 | 75..300 | от светло-коричневого до тёмно-красного | |
Кирпич пустотелый «сверхэффективный» (НПО «Керамика») | 1100..1150 | 6..10 | 15..50 | 0,25..0,26 | 50..150 | оттенки красного | |
Кирпич облицовочный | 1300..1450 | 6..14 | 25..75 | 0,3..0,5 | 75..250 | от белого до коричневого | |
Кирпич лицевой «сверхэффективный» (НПО «Керамика») | 1100..1150 | 43..45 | 25..75 | 0,25..0,26 | 125, 150 | от белого до коричневого | |
Кирпич облицовочный глазурованный или ангобированный | 1300..1450 | 6..14 | 25..75 | 0,3-0,5 | 75..250 | в зависимости от желания заказчика | |
Кирпич клинкерный | 1900..2100 | 5 | 50..100 | 1,16 | 400..1000 | от желтого до тёмно-красного | |
Кирпич печной шамотный | 1700..1900 | 8 | 15..50 | 0,6 | 75..250 | от светло-жёлтого до тёмно-красного |
Кирпич полнотелый Полнотелый кирпич – материал с малым объемом пустот (меньше 13%). Применяется для кладки внутренних и внешних стен, возведения колонн, столбов и других конструкций, несущих помимо собственного веса дополнительную нагрузку. В силу того, что этот материал используют преимущественно для возведения несущих элементов зданий, распространены другие его названия – «строительный», «обычный», «рядовой». Он должен обладать высокой прочностью на изгиб, на сжатие (если конструкция сильно нагружена, то можно заказать марку М250 и даже М300), быть морозостойким. По ГОСТУ максимальная марка по морозостойкости такого кирпича – F50, но можно встретить и кирпич марки F75. Пористость определяет теплоизолирующие свойства, качество сцепления с кладочным раствором, а заодно и впитывание влаги при смене погоды. Водопоглощение обычного кирпича должно быть более 8%, а на рынке присутствует материал, у которого эта величина достигает 20%. Обратите внимание: сопротивление теплопередаче полнотелого кирпича невелико. Поэтому наружные стены, полностью выложенные из этого материала, требуют дополнительного утепления. Кирпич пустотелый Пустотелый кирпич применяют для кладки облегченных наружных стен, перегородок, заполнения каркасов высотных и многоэтажных зданий. На самом деле «имен» у этого кирпича много. В различных анонсах его называют «дырочным», «щелевым», «экономным» («экономичным») и «самонесущим». Из последнего названия видно, что он используется преимущественно для ненагруженных конструкций. Отверстия в пустотелом кирпиче могут быть как сквозные, так и закрытые с одной стороны; по форме – круглые, квадратные, прямоугольные и овальные; по расположению – вертикальные и горизонтальные. Необходимо учитывать, что материал с горизонтальными отверстиями менее прочен (М25..М100). За счет того, что пустоты составляют значительную часть объема (более 13%), на изготовление пустотелого кирпича уходит меньше сырья, чем на изготовление полнотелого. Отсюда – и относительно скромная цена, и название – «экономичный». Кроме того, замкнутые объемы сухого воздуха повышают теплоизолирующие свойства материала. Нужно только следить, чтобы кладочный раствор был достаточно густой и не заполнял отверстия, иначе этим преимуществом нельзя будет воспользоваться. Разумеется, на степень проникновения раствора влияет и размер самих щелей. Для улучшения теплотехнических характеристик еще на этапе производства стараются добиться повышенной пористости сплошной части кирпича: при подготовке глины в нее добавляют торф, мелко нарезанную солому, опилки или уголь, которые при обжиге выгорают, образуя маленькие пустоты в глиняном массиве. Зачастую полученный таким образом кирпич называют «легким» или «сверхэффективным». Кирпич облицовочный Облицовочный, он же «лицевой» и «фасадный», используют при облицовке зданий. Стандартные размеры у него такие же, как у рядового, – 250x120x65 мм. Некоторые производители предлагают фасадный кирпич уменьшенной ширины (85 мм вместо 120). Как правило, фасадный кирпич – пустотелый, а следовательно, его теплотехнические характеристики достаточно высоки. По нормативам, облицовка обязана обладать хорошей морозостойкостью и «презентабельным» внешним видом. Цвет должен быть ровным, грани – гладкими, формы – точными. Не допускается наличие трещин и расслоения поверхности. Подбирая составы глиняных масс и регулируя сроки и температуру обжига, производители получают самые разнообразные цвета. Затраты на кирпичную облицовку больше, чем на оштукатуривание, но при правильном выборе материала «керамический» фасад не потребует обновления гораздо дольше, чем штукатурка. Интересен облицовочный фактурный (рельефный) кирпич Его ложковая и тычковая поверхности имеют рисунок. Это может быть просто повторяющийся вдавленный рельеф, а может быть и обработка под «мрамор», «дерево», «антик» (фактурный с потертыми или нарочито неровными гранями) – на выбор заказчика. Фасонный кирпич по-другому называют фигурным, что говорит само за себя. Отличительные признаки такого кирпича – скругленные углы и ребра, скошенные или криволинейные грани. Именно из таких элементов без особых сложностей возводят арки, круглые колонны, выполняют декор фасадов. Существуют специальные элементы для подоконника и карнизов. Подвид фасонного – лекальный кирпич, форма которого выполняется на заказ, по предоставленному лекалу. Кирпич облицовочный глазурованный или ангобированный Для получения кирпича с блестящей цветной поверхностью на обожженную глину наносят глазурь (специальный легкоплавкий состав, в основе которого – перемолотое в порошок стекло), а затем проводят вторичный обжиг уже при более низкой температуре. После этого образуется стекловидный водонепроницаемый слой, обладающий хорошим сцеплением с основной массой и, как следствие, повышенной морозостойкостью. Глазурованный кирпич позволяет выкладывать мозаичные панно как в помещении, так и со стороны улицы. Технология получения ангобированного кирпича (его еще называют «двухслойным» или «цветным») отличается тем, что цветной состав наносят на высушенный сырец и обжигают только один раз. Само декоративное покрытие тоже другое. Ангоб состоит из белой или окрашенной красителями глины, доведенной до жидкой консистенции. Если температура обжига подобрана правильно, он дает непрозрачный, ровный слой матового цвета. Глазурованный и ангобированный кирпич применяют при оригинальной дизайнерской облицовке внешних и внутренних стен. Широкая цветовая гамма позволяет реализовать фактически любую идею оформления. К внешнему виду глазурованного и ангобированного кирпича предъявляют приблизительно одинаковые требования. На цветной поверхности не должно быть наплывов и трещин, пузырьков и вздутий. Зазубрины и щербинки допускаются, но в очень малом количестве (не более 4 штук). То же относится к пузырькам и черным точкам – «мушкам» (не более 3). Нужно учитывать, что цветной слой обоих кирпичей достаточно хрупок – вероятно, в силу этого они не слишком востребованы. Их изготовливают в основном за рубежом и на заказ, однако есть производители и в России – это челябинский завод «Кемма», красноярский «Красноярскстройматериалы» и др. Ангобированныи кирпич с покрытием белого цвета выпускает завод «Победа Кнауф», цветной материал с повышенной пустотностью (до 43%) – НПО «Керамика». Кирпич клинкерный Применяют для облицовки цоколей, мощения дорог, улиц, дворов, полов в цехах промышленных зданий, облицовки фасадов. Погруженный полностью в воду, клинкерный кирпич выдерживает минимум 50 циклов попеременного замораживания/оттаивания, а что касается прочности, то ниже марки М400 его просто не выпускают. Такие характеристики обеспечиваются большой плотностью кирпича, которая достигается благодаря особому сырью и особой технологии. В производстве данного вида материала используют тугоплавкие глины. Их обжигают до спекания при значительно более высоких температурах, чем принято для изготовления обычного строительного кирпича. Материал получается дорогой, и его в использование целесообразно там, где эксплуатация элементов строений или дорожных покрытий проходит в самых жёстких условиях. Кирпичное мощение дорожек не очень популярно в России, поэтому чаще клинкер используют для облицовки фасадов – отделка долгое время не нуждается в ремонте, грязь и пыль практически не проникают в структуру поверхности, да и вариаций цветов и форм – масса. Недостаток только один: в силу высокой плотности клинкер обладает повышенной теплопроводностью. Кирпич шамотный Чтобы избежать быстрого разрушения кладки, контактирующей с открытым огнем, необходим кирпич, способный выдерживать высокие температуры. Его называют «печным», огнеупорным и шамотным. Данный материал выдерживает температуры свыше 1600°C. Делают такой кирпич из шамота – огнеупорной глины. Кстати, ту же глину добавляют в кладочный раствор, чтобы печь не развалилась от воздействия пламени. Изготавливают шамотный кирпич классической, а также трапециедальной, клиновидной и арочной формы. Транспортировка и хранение Одним из реальных источников появления брака керамического кирпича (трещин, половняка, отбитостей и сколов) является его некоректная транспортировка. Зачастую можно наблюдать, как кирпич (даже относительно дорогой – облицовочный) перевозят навалом и разгружают, как щебень, самосвалом. Некондиция при таком способе транспортировки может достигать 20% от начального объёма. «Цивилизованным» способом является перевозка кирпича на поддонах. Завод-изготовитель, как правило, подобным образом и отпускает потребителю свою продукцию, а поддоны либо продает, либо сдает в аренду; рассматриваются варианты доставки на поддонах заказчика. Керамический кирпич является обжиговым материалом, имеющим неплохую атмосферостойкость и это допускает его приобретение впрок (в том числе и зимой). Хранение керамического кирпича желательно осуществлять под навесом (исключающим прямое попадание на него атмосферных осадков), в штабелях, с вентиляционными зазорами в кладке и проходами между штабелями. Хранение «россыпью» ни в коем случае на пользу кирпичу не пойдет. Общие рекомендации При покупке кирпича требуйте сопроводительные документы: сертификат или паспорт на продукцию. При отсутствии этих документов, на кирпич лучше не соблазняться. Если не хотите «топить улицу», не делайте наружные стены толщиной меньше, чем в 2,5 кирпича (то есть 64 см), иначе тепло будет уходить из дома. При покупке импортного кирпича учтите, что европейские стандарты не всегда совпадают с отечественными по размерам, морозостойкости, прочностным показателям. Помните об этом при соместном использовании импортного и российского кирпича. Также необходимо учитывать, что толщина отечественных железобетонных элементов (перемычки, плиты перекрытия) кратна высоте отечественного кирпича. Сколько нужно кирпича, чтобы построить двухэтажный дом? Произведём расчёт для двухэтажного дома со стенами размерами 8x8 м при высоте потолков в 3 м. 1. Определяем длину наружных стен: 8 м · 4 = 32 м;2. Высота потолка – 3 метра, тогда высота стен двухэтажного дома – 6 метров, значит, площадь наружных стен: 32 м · 6 м = 192 м2; 3. Выбираем кладку в 2,5 кирпича, тогда толщина стен будет равняться 64 см, хотя по каждому отдельно взятому проекту это значение придется высчитывать индивидуально, исходя из конструктивных особенностей здания, веса перекрытий и т.п. При этом кладку в два кирпича будем выполнять из двойного рядового кирпича и один ряд (в полкирпича) - из одинарного лицевого. Находим усредненный расход кирпича: Табл. 2. Усредненный расход кирпича на 1 м2 кладки |
Вид кладки | Толщина кладки, см | Размер кирпича | Кол-во без учёта растворных швов, шт | Кол-во с учетом растворных швов, шт |
В 0,5 кирпича | 12 | одинарный полуторный двойной |
61 45 30 |
51 39 26 |
В 1 кирпич | 25 | одинарный полуторный двойной |
128 95 60 |
102 78 52 |
В 1,5 кирпича | 38 | одинарный полуторный двойной |
189 140 90 |
153 117 78 |
В 2 кирпича | 51 | одинарный полуторный двойной |
256 190 120 |
204 156 104 |
В 2,5 кирпича | 64 | одинарный полуторный двойной |
317 235 150 |
255 195 130 |
Если количество кирпича считать с учетом растворных швов, то получим: 192 · 104 = 19 968 штук двойного рядового или 192 · 204 = 39 168 штук одинарного рядового кирпича плюс 192 · 51 = 9 792 штуки лицевого одинарного кирпича. С учетом действующих цен, весь кирпич будет стоить 5..6 тысяч долларов.
Также можно посчитать, во сколько обойдется дом с готовой отделкой. Строители подсчитали, что 1 м2 в кирпичном доме стоит 350…400 долларов. То есть нужно умножить общую площадь дома (128 м2) на 350 долларов. Таким образом наш дом с отделкой будет стоить 45 тысяч долларов. Видно, что цена на кирпич от общей стоимости дома составит 10..12%, остальные 40 тысяч – инженерное оборудование и внутренняя отделка здания.
Отсюда напрашивается вывод – экономить на кирпиче и его качестве совершенно невыгодно.
Страницы
- « первая
- ‹ предыдущая
- 1
- 2
- 3
- 4
- 5
- 6
- 7
- 8
- 9
- …
- следующая ›
- последняя »