![]() Виды
|
Нефтяной битум является общепринятым вяжущим для строительства и ремонта автомобильных дорог. Однако‚ с технологической точки зрения‚ его следует применять при минимально возможной вязкости‚ что может быть достигнуто тремя принципиальными способами:
Первый способ используется обычно для производства горячих смесей с предварительным нагревом исходных минеральных материалов или розливом горячего битума на холодную поверхность при производстве подгрунтовки или устройстве поверхностной обработки. Этот способ имеет достоинства и недостатки. К достоинствам следует отнести возможность получения конгломерата (асфальтобетона) с высокой прочностью при использовании высоковязких битумов для дорог с тяжелым и интенсивным движением‚ а к недостаткам – затраты энергии на нагрев минеральных материалов при производстве горячих смесей‚ ограниченный период времени на устройство конструктивных слоев дорожной одежды и отрицательное воздействие на окружающую среду в процессе всего цикла производства работ. Второй способ‚ как правило‚ дороже из-за весьма дорогостоящих растворителей‚ которые за относительно короткий период времени должны испариться‚ что приводит к загрязнению окружающей среды и к повышенной пожароопасности при производстве работ. Третий способ‚ с использованием битумных эмульсий‚ не требует нагрева и может использоваться с холодными и даже влажными минеральными материалами‚ что позволяет снизить расход энергоносителей до 40% по сравнению с традиционными «горячими» технологиями. Принципиальная схема производства битумной эмульсии Эмульсия – неоднородная‚ термодинамическая неустойчивая система с двумя или несколькими жидкими фазами‚ представляющими одну постоянную жидкую фазу (дисперсионную среду) и‚ по меньшей мере‚ вторую жидкую фазу‚ рассеянную в первой в форме мелких капелек (дисперсная фаза). В зависимости от формы‚ битумные эмульсии классифицируются на прямые и обратные. Прямые эмульсии – это когда битум в виде мелких капелек (от 1 до 20 мк) находится в водной среде. Обратная эмульсия – это когда вода в виде мелких капелек находится в битумной среде. В дорожной практике наибольшее применение находят прямые битумные эмульсии. В зависимости от требуемых технологических и эксплуатационных свойств связующего материала эмульсии могут быть приготовлены на битумах различной вязкости как с использованием различных добавок (растворители‚ ПАВ‚ полимеры)‚ так и без них. При этом в зависимости от назначения и условий применения могут приготавливаться эмульсии с различной скоростью их распада и устойчивостью при транспортировке и хранении. Относительно низкая вязкость прямых битумных эмульсий‚ обусловленная наличием водной среды (от 31 до 50%)‚ обеспечивает хорошую способность обработки каменных материалов без их сушки и нагрева. Такие технологические свойства битумных эмульсий обусловливают благоприятное их применение в дорожном строительстве с позиций охраны труда дорожных рабочих и охраны окружающей среды. В зависимости от применяемых эмульгаторов эмульсии могут быть анионного и катионного видов. При этом за последние годы в мировой практике дорожного строительства производятся и используются главным образом (почти 100%) эмульсии катионного вида‚ как наиболее универсальные и обеспечивающие достаточную адгезию вяжущего к поверхности минеральных материалов кислой и основной природы. За более чем 60-летний период производства битумных эмульсий катионного вида за рубежом в совершенстве отработаны различные составы и технологии их применения в дорожном строительстве и налажен промышленный выпуск большого ассортимента эмульгаторов для различных составов эмульсий применительно к их назначению. Наибольший опыт в теоретических разработках и в практическом использовании битумных эмульсий накоплен во Франции‚ которая считается мировым лидером в этих вопросах и где более 30% от общего объема органических вяжущих для дорожных целей применяется в эмульгируемом виде. В России в середине 60-х годов на основании научно-исследовательских работ и небольшого опыта практического применения были разработаны технические и нормативные документы по приготовлению и использованию битумных эмульсий в дорожном строительстве. Однако главным образом эти документы отражали вопросы применения эмульсий анионного вида‚ так как химическая промышленность России и в целом Союза ССР не производила катионные эмульгаторы применительно к дорожному строительству. За весь этот период отечественной машиностроительной промышленностью не был налажен выпуск всего комплекта оборудования для эмульсионных баз‚ и только на энтузиазме отдельных специалистов и коллективов дорожников создавались такие базы для производства эмульсий анионного вида. За последние годы в условиях рыночных отношений и открытости границ в России и странах СНГ целый ряд дорожных организаций начал создавать базы по производству катионных битумных эмульсий‚ главным образом‚ на основе импортного оборудования с использованием импортных эмульгаторов. Наряду с этим‚ ряд наших заводов‚ и в частности АО «Дормаш» (г. Верхний Уфалей)‚ начал выпуск комплекта оборудования для приготовления битумных эмульсий. Несмотря на то‚ что государственный стандарт на эмульсии битумные дорожные действует с 1982 года (ГОСТ 18659-81)‚ первые технические условия на промышленный выпуск отечественных эмульгаторов катионного вида для дорожных целей были разработаны в 1996 году фирмой «Дорос» (г. Ярославль) и фирмой ЗАО «Амдор» (Санкт-Петербург)‚ испытания проб которых показали их конкурентную способность по отношению к лучшими зарубежным аналогам. Промышленные установки по производству битумных эмульсий имеют производительность‚ как правило‚ от 5 до 40 т/ч. Производство эмульсий обычно осуществляется с помощью коллоидных мельниц‚ основными характеристиками которых являются:
При этом в разных установках подготовка дисперсионной среды (водной фазы) производится либо заранее в отдельной емкости и в готовом виде подается параллельно с битумом в коллоидную мельницу‚ либо с помощью насосов-дозаторов все компоненты эмульсии в определенной пропорции‚ согласно рецепту‚ подаются в коллоидную мельницу с постоянным измерением водородного потенциала рH как дисперсионной среды‚ так и готовой эмульсии. Прямые битумные эмульсии катионного вида применяются для следующих видов дорожных работ:
Устройство подгрунтовкиЭмульсия наносится разбрызгиванием равномерным слоем на очищенную поверхность основания (покрытия) с помощью гудронатора из расчета 0‚20–0‚30 л/м2 в зависимости от состояния обрабатываемой поверхности. По подгрунтованной полосе нельзя открывать движение‚ так как это может привести к авариям. Однако движение построечного транспорта при устройстве слоя покрытия не вызывает опасений. После распада эмульсии и испарения воды на поверхности остается равномерная тонкая пленка битума‚ исключающая явление сдвига при уплотнении уложенной по ней асфальтобетонной или подобной ей смеси и обеспечивающая хорошее сцепление между слоями дорожной одежды. Для подгрунтовки используется быстрораспадающаяся эмульсия 50-процентной концентрации следующего ориентированного состава:
Подгрунтовка наносится за 1–3 часа до начала устройства слоя покрытия из условия времени распада эмульсии и испарения воды. Следует избегать того‚ чтобы обработанная поверхность длительное время оставалась открытой‚ так как из-за пыли и загрязнения связующая роль подгрунтовки ухудшится. При относительно небольшой скорости технологического потока устройства асфальтобетонного слоя целесообразно иметь в наличии высокоманевренный минигудронатор небольшой прозводительности. В прохладную и влажную погоду эмульсии целесообразно подогревать до 40–50°С. Приготовление холодных эмульсионно-минеральных смесейХолодные эмульсионно-минеральные смеси предназначены для устройства конструктивных слоев дорожных одежд‚ в том числе покрытий на автомобильных дорогах III–IV категорий. Верхние слои оснований допускается устраивать из эмульсионно-минеральных смесей и на автомобильных дорогах II категории. Для устройства оснований рекомендуются смеси с максимальным размером зерен до 40 мм и содержанем частиц менее 0‚071 мм до 4%‚ а для покрытий с максимальным размером зерен до 20 мм и содержанием частиц менее 0‚071 мм – до 9%. При этом глинистых частиц не должно быть более 2 %‚ а содержание органических примесей в составе минеральной части смеси не должно превышать 0‚2% по массе. Ориентировочный состав эмульсий следующий:
Минеральная часть смеси должна иметь непрерывную плавную гранулометрию. Анализ зернового состава минеральной части смеси для эмульсионно-минеральных материалов‚ по нормативным и информационным документам России‚ Белоруссии‚ Франции и Финляндии‚ позволил составить кумулятивную таблицу гранулометрии минеральной части таких смесей (табл. 1).
Смеси‚ в зависимости от назначения‚ могут быть щебеночно-песчаные или гравийно-песчаные. Для обеспечения хорошей обрабатываемости минеральная смесь должна иметь влажность порядка 2–4%. В качестве исходного битума для эмульсий предпочтение следует отдавать нефтяным битумам из малопарофинистых высокосмолистых тяжелых нефтей‚ обеспечивающих стабильность свойств вяжущего во времени. Из отечественных битумов предпочтение следует отдавать битумам марки БДУ производства АО «Битран» (г. Ухта). Условная вязкость исходного битума должна быть в пределах 200–300 ед. пенетрации. При этом в зависимости от срока хранения готовой смеси в штабеле и содержания мелких частиц в минеральной части смеси при производстве эмульсии следует вводить пластификаторы из условия достижения и сохранения требуемой удобоукладываемости приготовленной смеси в течение необходимого периода времени. В качестве пластификатора могут использоваться маловязкие гудроны‚ топочный мазут или моторное топливо. Количество пластификатора устанавливают опытным путем при лабораторных испытаниях. Эмульсия должна быть медленнораспадающаяся с содержанием битума 60–65% по массе. В случае неудовлетворительного сцепления вяжущего с каменным материалом следует дополнительно в эмульсию вводить ПАВ. Состав эмульсии в каждом конкретном случае уточняется в лаборатории. Расход эмульсии для приготовления холодных смесей составляет 5‚5–6‚5% по массе минеральных материалов. В каждом конкретном случае расход эмульсии уточняется на стадии проектирования состава смеси. Готовая смесь должна отвечать требованиям табл. 17 ВСН 115-75 (Технические указания по приготовлению и применению дорожных эмульсий. М.‚ 1976 г.). Работы по устройству конструктивных слоев из эмульсионно-минеральных смесей следует производить при температуре воздуха не ниже 5OС. Максимальная толщина слоя‚ укладываемого за один технологический цикл‚ должна составлять не более 10 см. Смесь укладывают асфальтоукладчиком или любым другим финишером‚ например автогрейдером. Уплотнение смеси целесообразно производить катками на пневмошинах с последующим выравниванием поверхности слоя 2–3 проходами катком с металлическими вальцами. В случае переувлажненной смеси ее после укладки следует подсушить‚ а затем производить уплотнение. Движение по уплотненному слою можно открывать сразу же‚ но при этом в течение нескольких дней ограничивают скорость движения транспорта до 30–40 км/ч. Устройство последующих конструктивных слоев или поверхностной обработки допускается после формирования слоя из эмульсионно-минеральной смеси‚ но не ранее чем через 5–7 суток при сухой теплой погоде. Работы следует вести в соответствии с положениями СНиП 3.06.03-85 и ВСН 115-75. Устройство оснований по способу холодного ресайклингаХолодный ресайклинг представляет собой укрепление (стабилизацию) грунтов‚ каменных материалов и асфальтовой крошки различными вяжущими‚ в том числе битумной эмульсией путем предварительного фрезерования и смешения на дороге. Технология холодного ресайклинга весьма эффективна при ремонте и реконструкции существующих дорог‚ когда старая дорожная одежда сфрезеровывается частично или на всю глубину с помощью ресайклера и материал используется для укрепления вяжущим‚ в частности‚ битумной эмульсией в качестве основания. По оценкам специалистов‚ холодный ресайклинг на 20% дешевле традиционной технологии ремонта и на 40–50% сокращает затраты времени. Для получения достаточно плотного и прочного укрепленного основания кривая гранулометрического состава смеси отфрезерованного материала должна быть плавной и находиться в пределах‚ указанных в табл. 2.
Для стабилизации по способу холодного ресайклинга используются средне- или медленнораспадающиеся эмульсии с содержанием битума порядка 60–65%. Выбор исходного битума‚ концентрацию эмульсии и ее содержание в смеси осуществляют в каждом конкретном случае на основании предварительных лабораторных испытаний и требований к конечному материалу. Ориентировочный расход 60-процентной эмульсии находится в пределах 3‚5–5‚5%. Устройство покрытия (основания) по способу пропиткиДля устройства слоев дорожных одежд по способу пропитки используют среднераспадающуюся эмульсию. Устройство конструктивных слоев дорожной одежды по способу пропитки следует производить при температуре воздуха не ниже 5°C. При этом при температуре воздуха ниже 10°C эмульсии необходимо подогревать до температуры 40–50°C. Ориентировочный состав эмульсии следующий:
Покрытие по способу пропитки следует устраивать из щебня изверженных пород марки не ниже 800 или осадочных и метаморфических пород не ниже 600. Щебень‚ используемый для устройства оснований‚ должен быть марки не ниже 600. Каменные материалы должны быть чистыми и не должны содержать частиц менее 1 мм больше‚ чем 3%. Количество эмульсии‚ необходимое для пропитки‚ назначается из расчета:
При применении известнякового щебня концентрация эмульсии должна быть 55–60%‚ а гранитного щебня – 60–65%. Размер фракций и расход щебня‚ а также порядок работы осуществляют в соответствии с положениями СНиП 3.06.03-85 и ВСН 115-75 в зависимости от толщины слоя пропитки. В каждом конкретном случае необходимо опытным путем уточнять расход эмульсии. Эмульсию следует разливать по влажному щебню. Устройство покрытий следует заканчивать за 5–7 суток до наступления осенних дождей. Поверхностную обработку можно устраивать через 3–5 дней после выполнения работ по пропитке. |
![]() Современное устойство
|
Устройство поверхностной обработкиПоверхностную обработку с использованием эмульсии устраивают на автомобильных дорогах II–IV категорий‚ как правило‚ на покрытиях из асфальтобетонных или подобных им смесей. Для устройства поверхностной обработки используют быстрораспадающуюся эмульсию с концентрацией 67–69%. Для приготовления эмульсий в Северо-Западном регионе России рекомендуется использовать битум марки БДУ 100/130. Ориентировочный состав эмульсии следующий:
Исходя из жесткости асфальтобетонных покрытий и наличия производимого щебня для поверхностной обработки с использованием эмульсий возможно применение прочного щебня фракций 10–15 мм и 15–20 мм. В связи с тем‚ что возможны закрупнение щебня‚ повышенные поперечные уклоны проезжей части и большой расход эмульсии при применении щебня фракции 15–20 мм‚ целесообразно использовать щебень фракции 10–15 мм. Щебень по форме зерен должен соответствовать группе 1‚ т. е. содержание зерен игловатой и лещадной формы не должно превышать 15% по массе. Замельчение и закрупнение фракции щебня 10–15 мм не должно нарушать правило Паво и Линкенхейля‚ когда d=0‚6Д (d – наименьший размер зерен‚ а Д – наибольший). По нормам Франции‚ содержание зерен лещадной и игловатой формы допускается на дорогах с малой интенсивностью движения до 20–25%‚ на дорогах с интенсивным движением – до 15%‚ а на дорогах с высокой интенсивностью движения – до 10% по массе щебня. Щебень должен быть очень чистым‚ что обсуловливает его тщательную мойку либо в процессе производства‚ либо на строительной площадке. Количество частиц‚ проходящих через сито 0‚5 мм‚ не должно быть больше 2% для дорог с малой интенсивностью движения‚ не более 1‚0% – для дорог с интенсивным движением и не более 0‚5% – для дорог с высокой интенсивностью движения. При этом в остатке менее 0‚5 мм не должно быть частиц менее 0‚005 мм более чем 0‚05%. Наличие глины исключается совершенно. Норма расхода щебня фракции 10–15 мм составляет 11‚5–13 кг/м2‚ а эмульсии – 1‚6–1‚8 л/м2. Перед устройством поверхностной обработки покрытие должно быть тщательно очищено от грязи и пыли. В необходимых случаях следует промывать покрытие водой. Перед розливом эмульсии поверхность покрытия не должна быть мокрой‚ но может быть слегка влажной. На подготовленную поверхность автогудронатором с хорошо прочищенными форсунками производят розлив эмульсии всего объема в один прием. Практические дозирования вяжущего в указанных выше объемах являются средними значениями для средних условий состояния покрытия. Сложность состоит в том‚ чтобы оценить конкретное состояние поверхности покрытия: «жирная» и гладкая поверхность‚ пористая‚ шероховатая и очень шероховатая поверхность. Отсюда и норма розлива эмульсии должна быть дифференцирована по отношению к среднему значению‚ равному 1‚7 кг/м2. В случае с гладкими и «жирными» поверхностями покрытия может быть уменьшение дозировки порядка на 10–20%. Во всех других случаях возможно увеличение нормы розлива на 10–20% от среднего значения‚ что позволит избежать негативных последствий‚ обусловленных пористой‚ шероховатой или покрытой микротрещинами поверхностью. В прохладную и пасмурную погоду (менее 20°C) предпочтительно производить розлив эмульсии при ее температуре 40–70°C. В жаркую сухую погоду (25°C и выше) специальный подогрев эмульсии не требуется. Щебнераспределитель должен следовать за гудронатором не позже чем через 20–40 с. Этот временной промежуток не следует увеличивать‚ так как‚ во-первых‚ это определяется временем распада эмульсии‚ а во-вторых‚ при деформированном (неровном) покрытии эмульсия может стекать в пониженные места. Особое внимание следует уделять сопряжениям на стыках. Не схватившийся во время обработки предыдущего участка щебень должен сметаться перед розливом эмульсии на последующем участке. Скорейшее распределение щебня за розливом эмульсии определяет качество будущего слоя поверхностной обработки и дневную производительность отряда на объекте. Уплотнение поверхностной обработки обеспечивает упаковку зерен щебня и их закрепление на поверхности покрытия посредством пленки вяжущего. Пневматические катки хорошо обеспечивают эти функции. Пневматические шины приспосабливаются к неровностям поверхности и не раздавливают зерна щебня. Этот эффект достигается при давлении в шинах от 7 до 8 бар и нагрузках от 2 до 2‚5 т на колесо за 3–5 проходов по следу со скоростью порядка 3 км/ч в начале укатки и со скоростью до 10 км/ч при последних проходах. В течение 1–2 суток следует ограничивать скорость движения транспорта для исключения выброса зерен щебня из несформировавшегося полностью слоя поверхностной обработки. В процессе формирования слоя необходимо тщательно следить за выбросом зерен щебня и вовремя производить их удаление. В противном случае‚ наличие незакрепленных зерен щебня на поверхности «коврика» провоцирует его разрушения и создает опасность для участников движения. Ямочный ремонт покрытий с использованием машин типа «РОСКО»Машины типа «РОСКО» работают по принципу подачи на ремонтируемый участок (в выбоину) эмульсии и щебня‚ обработанного эмульсией в специальной камере с большой скоростью‚ что обеспечивает плотную упаковку смеси‚ благодаря чему не требуется ее последующее уплотнение другими средствами. Машина типа «РОСКО» позволяет производить продувку выбоин сжатым воздухом‚ предварительную подгрунтовку места ремонта эмульсией и затем подавать обработанный эмульсией мелкий щебень для заделки выбоин и других подобных дефектных мест небольшой площади. Для технологии ямочного ремонта с использованием машин этого типа в Финляндии используются быстрораспадающиеся эмульсии‚ приготовленные на вязких битумах со значением пенетрации при 25°C порядка 110–130 ед. При производстве работ в холодное время года желательно применять эмульсию с температурой +30–60°C. Исходя из этого‚ состав эмульсии может быть следующий:
Кроме того‚ ямочный ремонт асфальтобетонных покрытий с использованием эмульсий может производиться способом пропитки либо с применением складируемых и нескладируемых эмульсионно-минеральных смесей. Для способа пропитки следует использовать щебень различных фракций в зависимости от глубины и площади поврежденных мест‚ при этом максимальный размер зерен щебня‚ как правило‚ должен составлять не более 20–25 мм. Состав битумных эмульсий для указанных способов ремонта аналогичен составам эмульсий‚ изложенных в соответствующих разделах данной статьи. |
Геотермальная энергетика — производство электроэнергии, а также тепловой энергии за счёт энергии, содержащейся в недрах земли.
Преимуществом геотермальной энергетики является ее практически полная безопасность для окружающей среды. Количество СО2, выделяемого при производстве 1 кВт электроэнергии из высокотемпературных геотермальных источников, составляет от 13 до 380 г (например, для угля он равен 1042 г на 1 кВт/ч).
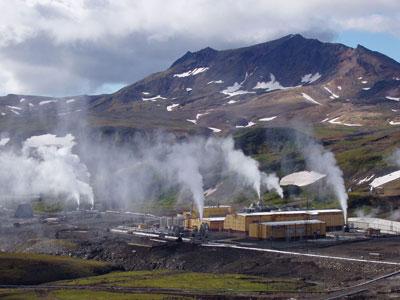
Однако тепло Земли очень "рассеянно", и в большинстве районов мира человеком может использоваться с выгодой только очень небольшая часть энергии. Из них пригодные для использования геотермальные ресурсы составляют около 1% общей теплоемкости верхней 10-километровой толщи земной коры, или 137 трлн. т у. т.
Источники геотермальной энергии по классификации Международного энергетического агентства делятся на 5 типов:
- месторождения геотермального сухого пара - сравнительно легко разрабатываются, но довольно редки; тем не менее, половина всех действующих в мире ГеоТЭС использует тепло этих источников;
- источники влажного пара (смеси горячей воды и пара) - встречаются чаще, но при их освоении приходится решать вопросы предотвращения коррозии оборудования ГеоТЭС и загрязнения окружающей среды (удаление конденсата из-за высокой степени его засоленности);
- месторождения геотермальной воды (содержат горячую воду или пар и воду) - представляют собой так называемые геотермальные резервуары, которые образуются в результате наполнения подземных полостей водой атмосферных осадков, нагреваемой близко лежащей магмой;
- сухие горячие скальные породы, разогретые магмой (на глубине 2 км и более) - их запасы энергии наиболее велики;
- магма, представляющая собой нагретые до 1300 °С расплавленные горные породы.
Опыт, накопленный различными странами (в том числе и Россией), относится в основном к использованию природного пара и термальных вод, которые остаются пока наиболее реальной базой геотермальной энергетики. Однако ее крупномасштабное развитие в будущем возможно лишь при освоении петрогеотермальных ресурсов, т. е. тепловой энергии горячих горных пород, температура которых на глубине 3. . .5 км обычно превышает 100 °С.
Геотермальное тепло можно утилизировать либо "непосредственно", либо преобразовывать его в электричество (посредством ГеоЭС), если температура теплоносителя достигает более 150 °С.
Геотермальная электростанция (ГеоЭС) — вид электростанций, которые вырабатывают электрическую энергию из тепловой энергии подземных источников.
Существует несколько способов получения энергии на ГеоТЭС:
- прямая схема: пар направляется по трубам в турбины, соединённые с электрогенераторами;
- непрямая схема: аналогична прямой схеме, но перед попаданием в трубы пар очищают от газов, вызывающих разрушение труб;
- смешанная схема: аналогична прямой схеме, но после конденсации из воды удаляют не растворившиеся в ней газы.
Сегодня уже в 80 стран мира в той или иной степени используется геотермальное тепло. В большей части из них, а именно в 70 странах, утилизация этого вида природного тепла достигла уровня строительства теплиц, бассейнов, использования в лечебных целях и т.д. А ГеоТЭС имеются примерно в 25 странах. Потенциал геотермальной энергетики в мире рассмотрен на рисунке.
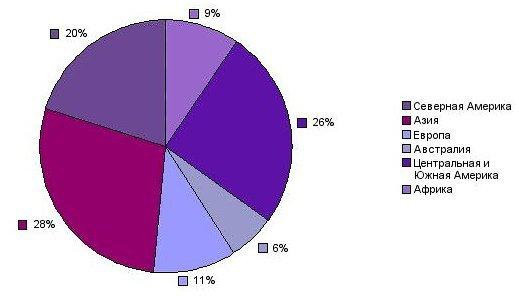
Сегодня ГеоТЭС производят около 54613 ГВт/ч в год. Современные объемы электроэнергии, получаемой благодаря этой технологии, достаточны для удовлетворения потребностей в электроэнергии 60 млн. человек, т. е. 1% населения планеты. Суммарная мощность существующих геотермальных систем теплоснабжения оценивается в 75900 ГВт / ч.
Россия не входит даже в первую десятку производителей электрической и тепловой энергии из геотермальных источников, и это несмотря на то, что запасы геотермальной энергии в России огромны и, по оценкам экспертов, в 10-15 раз превышают запасы органического топлива в стране. Одновременно, основные геотермальные источники в России расположены экономически невыгодно: Камчатка, Сахалин и Курильские острова отличаются слабой инфраструктурой, высокой сейсмичностью, малонаселенностью, сложным рельефом местности.
С экономической точки зрения в нашей стране наиболее интересными являются геотермальные ресурсы Краснодарского и Ставропольского краев, Калининградской области, где имеются запасы горячей воды с температурой до 1200Со. Запасы геотермального тепла имеются и на Чукотке, часть из них уже открыта и может активно использоваться для энергообеспечения близлежащих городов и поселков. На Северном Кавказе хорошо изучены геотермальные месторождения с температурой в резервуаре от 70 до 1800Со, которые находятся на глубине от 300 до 5000 м. Здесь уже в течение длительного времени используют геотермальные ресурсы для теплоснабжения и горячего водоснабжения в сельском хозяйстве, промышленности и в быту. Приморье, Прибайкалье, Западно-Сибирский регион также располагают запасами геотермального тепла, пригодного для широкомасштабного применения в промышленности и сельском хозяйстве и, конечно, для теплоснабжения городов и поселков.
По мнению экспертов, в последние годы в России наблюдается поворот к использованию геотермальных источников в энергетической отрасли. Вместе с тем, рассматривая текущее и перспективное производство электроэнергии на основе возобновляемых источников, следует отметить, что геотермальная энергия к началу века от общего количества вырабатываемой электроэнергии не превосходила 0.15 % и лишь к 2010 г. хотя и увеличится на треть, но не превысит 0.2 % с общей выработкой на уровне 7 ТВт/ч.
Подробную информацию о рынке геотермальной энергетики Вы можете почерпнуть из готового отчета о маркетинговом исследовании рынка геотермальной энергетики Research.Techart.
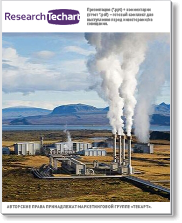
Маркетинговое исследование российского рынка геотермальной энергетики (вер.2)
Отчет об исследовании состоит из 10 частей.
В первой части разобраны основные понятия и определения, используемые в отчете, а также приведены общие сведения о геотермальной энергетике, ее преимуществах и недостатках.
Во второй части представлен обзор мирового рынка альтернативной энергетики, современное состояние составляющих его отраслей и перспективы их развития, рассмотрены направления и объем инвестиций в данной сфере.
В третьей части приведен обзор мировой отрасли геотермальной энергетики, его потенциал, количественные характеристики, лидеры отрасли, структура и т.п.
В четвертой части подробно рассмотрен российский рынок альтернативной энергетики: его потенциал, факторы развития, реализуемые проекты, существующие разработки и производимая продукция, государственные механизмы поддержки отрасли, направления и объем инвестиций и др. Раздел содержит сведения об основных участниках рынка — кадрах, разработчиках, производителях, поставщиках, проектно-монтажных организациях и ассоциациях. Были проанализированы существующая и перспективная структура спроса на альтернативные энергосистемы, выделены основные потребляющие сегменты.
Пятая часть - это анализ современного состояния отрасли геотермальной энергетики. В разделе содержатся данные о реализованных, реализуемых и планируемых проектах в данной сфере, о проблемах отрасли. Отдельно проанализирован потенциал отрасли.
Шестая часть содержит данные о государственном регулировании отрасли: федеральных и региональных программах регулирования сектора.
Седьмая часть полностью посвящена анализу инвестиций в отрасль: их объемам, структуре и направлениям вложений. Были рассмотрены основные финансовые показатели реализуемых в настоящее время проектов.
Восьмая часть — характеристика участников рынка: разработчиков и производителей геотермального оборудования.
В девятой части приведены оценки перспектив развития отрасли.
И, наконец, десятый раздел ориентирован на потенциальных участников рынка и инвесторов: в ней рассмотрены все особенности реализации проектов в геотермальной энергетике - возможности, риски, стоимость, возврат инвестиций и т.д. На основании проведенного анализа в заключении отчета сформулированы общие выводы по работе.
К отчету прилагается база данных компаний, представляющих российский сектор геотермальной энергетики.
Заказать отчет по исследованию рынка геотермальной энергетики можно на сайте компании Research.Techart По тел. (495) 663-32-62 или 790-75-91#124 E-mail: [email protected]
Предположим, что, взвесив все плюсы и минусы, вы решили строить дом "на века" из натуральных экологически чистых материалов. Что же в таком случае предпочтительнее: кирпич или дерево?
Как отмечает "Новый дом", наряду с природным камнем и необожженной глиной именно эти строительные материалы являются самыми древними. В Библии есть упоминание о кирпиче как о строительном материале уже применительно ко времени расселения людей сразу после Великого Потопа, т.е. на заре сознательной истории человечества. "И сказали друг другу: наделаем кирпичей и обожжем огнем. И стали у них кирпичи вместо камней" (Ветхий завет. Бытие. Гл. 11-3).
Это — экологически чистый материал, получаемый обжигом натуральной глины, так же, как и глиняная посуда, из которой можно есть. Как известно, кирпич не горит. А стена, сделанная из него, "дышит", обладает большой инерционностью при сохранении и отдаче тепла, поэтому в таком доме в жаркую погоду прохладно, а в холодную — тепло. Кирпич — материал долговечный. Фотография, сделанная на раскопках древнего итальянского города Остия, построенного во 2-3 веке от Рождества Христова, свидетельствует о прекрасном состоянии кладки, которой почти 2000 лет. Именно там я с удивлением понял, что основные строительные технологии, предназначенные для комфортной жизни, по существу, не изменились. Разница лишь в том, что раньше все делалось вручную тысячами рабов, а сейчас широко применяются машины. В основном, все последние строительные достижения заключаются в открытии предварительно напряженного железобетона, позволяющего перекрывать огромные пролеты. Но это все для промышленных конструкций.
Уже в те времена при строительстве жилых домов применялись фундаментные блоки, перемычки арочного типа, кирпичная кладка, облицовка различными материалами, штукатурка и многое, многое другое. Надо сказать, что когда перед нами в 1996 году встала аналогичная задача — оказалось, что это крайне дорого и непросто.
Отмечу, что за рубежом при строительстве дорогих домов стараются использовать кирпич, специально для этого выпускаемый, максимально похожий на старинный — с намеренно состаренной поверхностью, имеющей неровности, шероховатости, неравномерную окраску. В итоге получается как бы "дом с историей". Это очень ценится. Люди, имеющие средства, стараются приобрести кирпич или камень с каких-либо древних развалин. Так, во Франции мне показывали дом, пол которого выложен каменными плитами, купленными при перестройке монастыря X века. Это не только предмет особой гордости хозяев, но и фактор, существенно поднимающий рыночную стоимость дома. Специалисты-психологи также считают, что такая неоднородная по фактуре и по цвету стена комфортнее воспринимается человеком. Оказывается, наши глаза "не любят" четких однообразных геометрических линий. Нам ближе неоднородность и переменчивость, встречающаяся в природе, поэтому так приятно смотреть на лес, море или облака. И поэтому мы устаем от строгой геометрии искусственных промышленных сооружений.
У нас пока все наоборот: кирпич стараются подбирать идеально ровный, гладкий и одинакового цвета. Однако уже появились первые линии по выпуску искусственно состаренного кирпича.
В пользу строительства из этого материала говорит и то, что сейчас и у нас есть по-настоящему хорошие фирмы, детально отработавшие все технологические особенности и приемы строительства кирпичной коробки. Именно это, к сожалению, пока отсутствует при строительстве коробки из дерева. Это, конечно, прекрасный материал. Сейчас из Швеции, Финляндии и Канады поступает довольно много предложений по продаже домов из бруса, которые, кстати, очень дороги за рубежом, прежде всего из-за безукоризненной экологической чистоты. Но беда в том, что у нас такие деревянные дома никогда не строились в качестве жилья высшего разряда. Есть только опыт возведения деревенских срубов и деревянных церквей. А это совсем не одно и то же. Доверять сборку шведского или финского брусового дома даже самой уверенной в себе нашей "шабашкиной" бригаде ни в коем случае нельзя, а тем более — строительной компании (эти вообще о деревенских избах только в сказках про Ивана-Царевича читали). В чем же тут фокус? Все эти дома имеют массу технологических закладных элементов для прокладки современнейших инженерных коммуникаций, специальные монтажные анкеры, требующие дополнительной натяжки древесины при ее высыхании после постройки дома, и многое, многое другое. Наши пока не имеют в этом даже малого опыта. Мне приходилось видеть, как при строительстве все это просто выбрасывалось как нечто лишнее, случайно попавшее в упаковку иностранных контейнеров. К сожалению, пока такие дома хорошо могут собирать только иностранные специализированные компании. Естественно, что в этом случае, с учетом доставки и стоимости рабочей силы, жилье будет очень дорогим, не уступая в цене кирпичному.
На что бы я рекомендовал обратить внимание при строительстве стен из кирпича. При закупке количество кирпича должно быть увеличено на 5-8% по сравнению с проектом. Это является нормой боя и брака, и заводы свято соблюдают эту цифру.
Строительство стен из облицовочного кирпича должно начинаться не ниже 50-70 см от поверхности земли. Иначе он начнет тянуть в себя влагу. Кроме того, чтобы избежать капиллярного подсоса влаги из. фундамента, должна быть устроена горизонтальная гидроизоляция. В древние времена ее делали из свинцовых листов. Сейчас используют рубероид, гидростеклоизол или иной гидроизоляционный материал. Допускается также слой "жирного" цементного раствора.
Во внутренних, а реже и наружных стенах размещаются вентиляционные каналы и дымоходы. Для кладки последних должен использоваться плотный (не щелевой) кирпич или специальные вентиляционные трубы. К сожалению, очень распространенной ошибкой неквалифицированных строителей является устройство дымоходов из щелевого кирпича. Поскольку в продуктах сгорания современных газовых котлов присутствуют весьма агрессивные газы, то довольно скоро стены начинают разрушаться, осыпаясь вниз, в результате чего дымоход или полностью забивается, или разрушается вместе со стеной. И то, и другое чревато серьезной аварией.
По окончании рабочей смены бригада должна обязательно закрывать верхнюю часть стены рубероидом или целлофаном. Если этого не делать, то, казалось бы, мелкое нарушение может привести к серьезным неприятностям. Например, возможно, что в перерыве работ пойдет дождь, вода заполнит полости щелевого кирпича и будет месяцами оттуда испаряться, оставляя на стенах пятна и разводы, длительное время невысыхающие. А если при этом еще и заморозок случится, то стены могут покрыться сетью трещин.
При любой остановке работ на длительный срок (более 1 месяца) необходимо производить консервацию выполненной части кирпичных стен. В дальнейшем это избавит от серьезных неприятностей.
Для повышения надежности конструкции я рекомендовал бы устраивать дополнительное армирование стены кладочной металлической сеткой, в особенности в "проблемных" местах. Стоит это копейки, а надежность перевязки швов увеличивается значительно.
Очень важно соблюдение нормативных размеров опирания плит перекрытий на стену. Сплошь и рядом это нарушается из-за того, что стена при возведении оказалась чуть-чуть, всего-то на несколько сантиметров, сдвинута от проектного положения. Плиты же имеют фиксированный размер. И часто получается, что в итоге плита просто висит в воздухе, чудом зацепленная за край стены. И не дай бог, чтобы в таком доме кто-то лишний раз топнул ногой — все может просто рухнуть.
При укладке плит есть еще один тонкий момент. Предварительно напряженные плиты перекрытий больших пролетов имеют так называемый строительный прогиб, т.е. на заводе они изготовлены с выгибом вверх для того, чтобы после укладки под воздействием собственного веса (плюс вес пола и мебели) плита приняла горизонтальное положение. Иногда, не зная этого, плиты укладывают прогибом вниз. Исправить этот дефект уже нельзя. И чтобы не произошло аварии, придется полностью разбирать перекрытие.
Что касается швов кирпичной кладки, то на них, как и на любой архитектурный элемент, существует определенная мода. У нас сейчас предпочитают углубленные внутрь швы натурального цвета. Игра теней делает их темными. За рубежом любят тонированные швы. В Англии и Голландии обычно применяют светлые оттенки (белые, светло-бежевые). Конечно, это вопрос вкуса.
При отделке кирпичных фасадов сейчас применяются различные штукатурные элементы, не только украшающие дом, но и подчеркивающие его архитектурные особенности. Они выполняются после окончания строительства крыши и обычно не входят в понятие "коробки дома", но очень важно, чтобы уже при строительстве кирпичных стен необходимые рельефные элементы или крепежные армирующие детали были заранее выполнены. Например, необходимо выложить все выступающие и рельефные детали кирпичом, чтобы потом толщина штукатурки по фасаду была достаточно равномерна. Это значительно увеличит ее долговечность. Конечно, для строителей проще выполнить какой-либо выступающий элемент только из штукатурки. Но при этом ее толщина в отдельных местах получается слишком большой, и под воздействием своего веса эта часть со временем может разрушиться.
Карта 5.1. Московская область. Загородные проекты, вышедшие на рынок
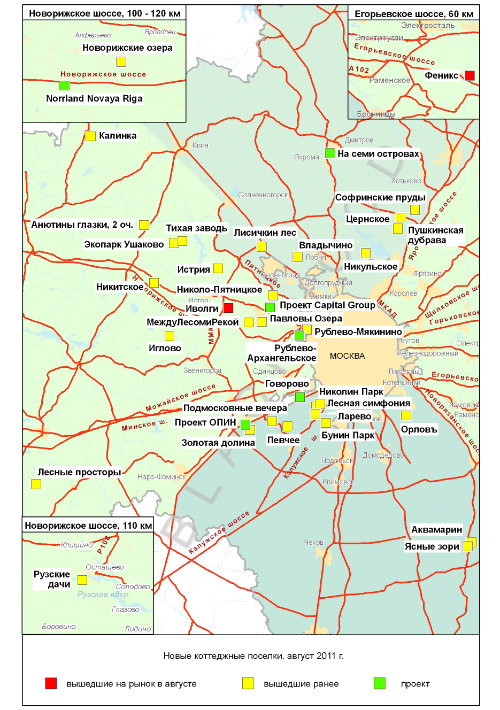
Источники: собственные данные компании Blackwood и открытые источники
В последний летний месяц 2011 г. рынок загородной жилой недвижимости оставался активным: выход новых поселков продолжился – в августе рынок пополнился двумя новыми проектами.
На Новорижском шоссе стартовали продажи в проекте «Иволги» - поселке бизнес-класса, расположенном в 35 км от МКАД, к продаже предлагаются готовые кирпичные дома площадью 204 - 272 кв. м на участках 10-12 соток. Поселок занимает территорию в 10 га и рассчитан на 70 домовладений. В первой очереди поселка уже построено 19 домов. Еще один новый проект, где на продажу предлагаются готовые дома, появился на Егорьевском ш. в 60 км от МКАД. В коттеджном поселке эконом-класса «Феникс» на продажу предлагаются домовладения с отделкой «под ключ» площадью 113-175 кв. м на участках 8-14 соток. Всего в поселке планируется строительство 220 домовладений.
В сентябре ожидается старт продаж еще в нескольких поселках, где также будут предлагаться коттеджи. Таким образом, мы можем наблюдать тенденцию постепенного снижения доли поселков с участками без подряда среди вновь выходящих на рынок проектов, которые доминировали в новом предложении последние три года.
Карта 5.2. Московская область. Организованные загородные поселки. Цены
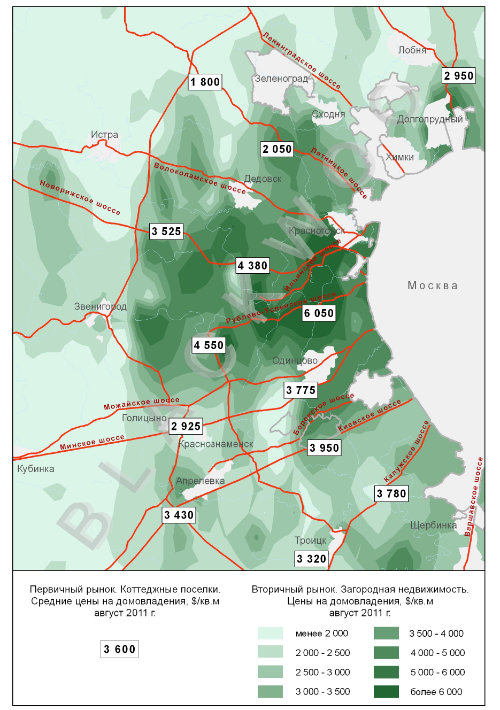
Источники: собственные данные компании Blackwood и открытые источники
Что касается ценовой ситуации на рынке загородного жилья, то в августе она оставалась стабильной без существенных сдвигов, с колебаниями в ту или иную сторону в зависимости от качества и стадии готовности проектов. В целом же август традиционно является последним месяцем летних скидок и специальных программ покупки, а многие застройщики анонсируют повышение цен в поселках с началом нового сезона.
Что касается цен в новых проектах, вышедших на рынок, то они оказались следующими: в поселке бизнес-класса «Иволги» на Новорижском ш. готовые дома площадью от 204 кв. м предлагаются по цене от 14,9 млн. рублей, в поселке эконом-класса «Феникс» на Егорьевском ш. цена на дома с отделкой «под ключ» варьируется от 5,2 до 7,6 млн. рублей.
Также в августе стало известно и том, что банк «ВТБ» через свою дочернюю структуру ООО «Эстейт Менеджмент» намерен продать земельный участок промышленного назначения на Дмитровском ш. в 25 км от МКАД. Общая площадь участка – 56,6 га, для него разработан план строительства логистического комплекса общей площадью 213 тыс. кв. м. Объект будет представлен на Международном инвестиционном форуме по недвижимости PROEstate 2011.
Предоставлено компанией BLACKWOOD
![]() |
– зимой, в период отопительного сезона, сравнительная влажность воздуха понижается, что тянет за собой рассыхание и растрескивание паркета;
– летом напротив: влажность излишне высока, и паркет, увеличивается в масштабах, начинает приподняться по краям.
Дабы этого не случалось, параметры микроклимата в помещение надо поддерживать в обусловленных пределах:
– относительная влажность воздуха не должна превосходить 60% и быть не ниже 40%;
– оптимальная температура для паркета от 15 до 25 градусов.
![]() |
При увеличенной влажности в комнате надо включить отопление или кондиционер, которые осушат воздух. Для постоянного контроля основных параметров микроклимата необходим прибор – термогигрометр.
Помимо влажности обезобразить паркет может самая обычная мебель, без какой трудно представить себе жилье. Зато возможно обезопасить деревянное покрытие, применяя мягкие войлочные набойки для стационарной обстановки и напольные коврики для передвижной.
Нужно помнить, что домашние животные тоже могут нанести большой вред паркету, но это не означает, что от домашних любимцев надо отказаться. Просто паркет требует немного больше внимания, а уход за ним больше стараний.
![]() |
Известным типом покрытия для деревянного пола является лак, предохраняющий его от стирания и наружных влияний. Для ликвидации загрязнений с лаковой поверхности есть специальные чистящие средства, выпускаемые в акцентированном виде или в аэрозольных упаковках. Оптимальным вариацией было бы использование лака и очистителя, изготовленные одинаковым производителем.
Как бы осторожно вы не относились к вашему новому полу, через некоторое время лак на некоторых зонах его поверхности стирается, показываются мелкие царапины и прочие дефекты. Предупредить это возможно, применяя защитные составы: водоразбавляемые или воскосодержащие. Они нетоксичны, безвредны для вас и животных. Нанести их можно не прибегая к помощи специалистов. Фактически, водоразбавляемые средства – разведенные лаки. Они создадут лишний защитный слой, усиливающий износостойкость паркета. Не менее результативны воскосодержащие полироли, но при их применении нужна дополнительная шлифовка.
![]() |
После 10-20 лет паркет можно обновить и даже целиком заменить лаковое покрытие. После циклевки на поверхность возможно нанести как лак, так и иной вид защиты, к примеру воск.
Покрытия полы, отделанные воском, призывают наиболее скрупулезного и плотного ухода, ведь стирается не лак, а само дерево. Воск выпускается двух типов: жидкий масляный и твердый, – и наносится тряпками или специальным шпателем со скругленными краями. Затем после покрытия воском полы полируются плоскошлифовальной машиной с белоснежным падом. Воск на паркет наносить необходимо пару раз в год, а натирать паркет два-три раза в неделю с помощью щетки или электрополотера.
Деревянная поверхность, отделанная маслом, обладает повышенной износостойкостью. Уход за таким деревянным полом – нетрудоемкое занятие. Необходимо лишь купить нужные для этого средства.
![]() |
![]() |
С отпечатками на деревянном полу от шоколада, обувного крема, резиновых следов от подошв, сажи осилит очиститель на основании керосина или спирта. Если ваши дети постановят внезапную выставку холстов на полу, цветной мел, грифель, фломастер, краски вы сотрете это все метиловым спиртом, разведенным водой в пропорции один к одному. Кровь смоется холодной водой, но не забывайте, что вслед за этой процедурой полы нужно насухо вытереть. А капли свечного воска или парафина, так как и налипшую жвачку, надлежит пунктуально соскрести, заморозив пакет льдом.
Помните, что средства для ухода и их своевременное использование существенно удлинят срок службы деревянного пола и сберегут его прекрасный наружный вид.
В этой статье вы познакомитесь с обзорами отраслевых растущих рынков, выявленных в результате статистической обработки данных российских федеральных ведомств.
Проведенный компанией ИАК «ВладВнешСервис» анализ данных официальной таможенной статистики за январь – март 2010 года позволил выделить растущие экспортные и импортные позиции на рынках строительных материалов.
На стабильных рынках импорта ситуация радостная – более 40 растущих позиций за первый квартал 2010 года! Среди них встречаем: земли шамотные или динасовые (код ТН ВЭД 2508700000); глиноземистый цемент (код ТН ВЭД 2523300000); строительную штукатурку (код ТН ВЭД 2520201000) и многие другие товары, необходимые при строительстве зданий и сооружений. Самый высокий объем продаж наблюдается у позиции «галька, гравий, щебень» (код ТН ВЭД 2517101000) – более 21 млн. долларов! Безусловно, без гравия и щебня в строительстве не обойтись, потому и видим мы такой растущий график:
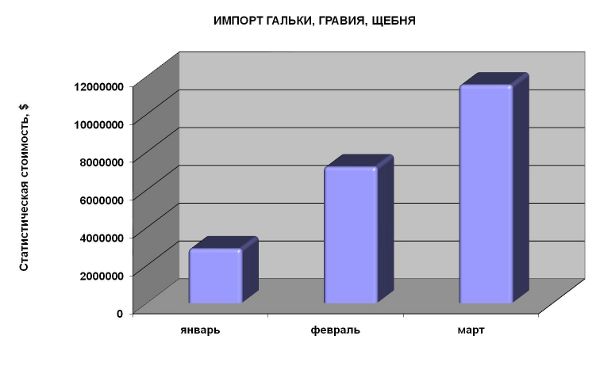
Но это не единственная позиция, показавшая такой активный рост в первом квартале 2010 года. Хорошим спросом пользуются жернова, точильные камни, шлифовальные круги и аналогичные изделия из природного камня (код ТН ВЭД 6804230000). Прирост по отношению к первому кварталу 2009 года составил 623 %!
На восстанавливающихся рынках импорта также видим неплохие тенденции. Например, рост импорта черепицы (код ТН ВЭД 6905100000) не добрал всего один процент до аналогичного периода прошлого года, а объемы продаж данного товара приближаются к 1 млн. долларов. Перспективной является еще одна позиция – «прочие камни полированные, декорированные или прошедшие прочую обработку, кроме резных, нетто-массой 10 кг или более» (код ТН ВЭД 6802991000). Объемы импорта полированных камней превышают 3 млн. 600 тыс. долларов, а прирост также не добрал один процент до уровня 1 квартала 2009 года.
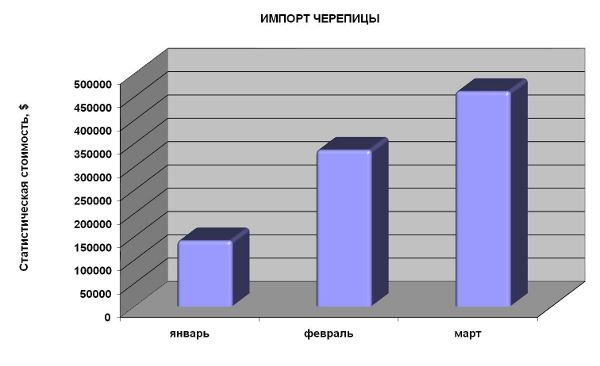
На стабильных рынках экспорта нас встречают старые знакомые – цементные клинкеры (код ТН ВЭД 2523100000), каждый месяц показывающие уверенный рост. Вот и в первом квартале 2010 года объемы продаж клинкеров превысили 80 млн. долларов, а прирост по отношению к аналогичному периоду 2009 года составил 2 579 %!
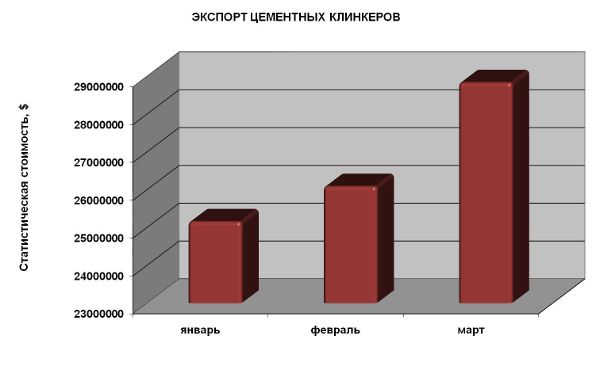
Лидером среди поставщиков отечественных клинкеров на запад является ЗАО "ОСКОЛЦЕМЕНТ" (Белгородская обл., г. Старый Оскол) – 45,39 % от всей доли рынка. На втором месте - ЗАО "МАЛЬЦОВСКИЙ ПОРТЛАНДЦЕМЕНТ" (Брянская обл.), занимающий 23,15 % на данном рынке.
На стабильных рынках экспорта также стоит отметить продажи портландцемента (код ТН ВЭД 2523290000), полевого шпата (код ТН ВЭД 2529100000), изделий из цемента, бетона или искусственного камня (код ТН ВЭД 6810990000), изделий из гипса или смесей на его основе (код ТН ВЭД 6809900000) и т.д.
На восстанавливающихся рынках экспорта выделим продажи плавикового шпата с содержанием фторида кальция 97 мас.% или менее (код ТН ВЭД 2529210000). Объемы продаж шпата росли весь первый квартал 2010 года, но суммарный объем не дотянул до значения аналогичного периода прошлого года 12 %.
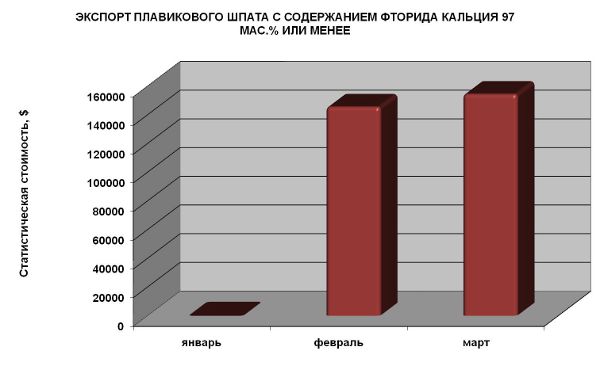
Экспортируют шпат три компании, среди которых лидером является ЗАО ФПК "БАЙКАЛПЛАВШПАТ" (Иркутская обл., г. Ангарск) – 55,49 % от всей доли рынка.
Предоставлено компанией ВладВнешСервис.
Сборные бассейны дают такую возможность тем, у кого есть даже небольшой участок земли – например дача.
Сборный бассейн не требует для установки каких-то особенных навыков и знаний, специальных подводов, инженерных коммуникаций и довольно дешев, прост в сборке и эксплуатации, надежен и прост.
Сборно-разборные бассейны изготовлены из специального пластика или тонкого стального листа, покрытого лаком и краской.
Бассейны бывают самых различных форм и размеров, каждый выберет для себя вариант по душе.
Диаметр большинства сборных бассейнов - 3-6 метров, однако в продаже есть и более крупные модели длиной до 12 метров (чаще всего они имеют овальную форму). Глубина чаши составляет от 1 до 1,5 метров, хотя детские бассейны могут быть и мельче.
Устройство бассейна:
Оцинкованный стальной лист, покрытый с двух сторон белым пластиковым слоем, внутрь вкладывается полимерное покрытие как правило синего или голубого цвета. Верхний и нижний профиль выполнен из пластика. К бассейнам обычно продают и полимерное покрытие для воды, чтобы она не засорялась. Внутренний пленочный материал устойчив к низким температурам, а особенность конструкции бассейна позволяет не сливать воду во время зимних месяцев. Необходимо лишь снять оборудование и убрать в отапливаемое помещение.
Бассейны высотой 1,5 метров необходимо частично (мин. На 0,75 м) заглубить. Вокруг этого бассейна необходимо устроить бетонный слой или утрамбованную подсыпку.
Монтаж небольшого сборного бассейна осуществляется несколькими этапами при помощи двух –трех человек:
1. Устройство площадки под дно бассейна (бетонная стяжка или утрамбованный песок);
2. Установка донных сегментов по заранее очерченному радиусу бассейна;
3. Установка стенок бассейна в донные сегменты, закрепление бортика центральным сегментом;
4. Укладка подкладочного материала;
5. Навешивание полимерного вкладыша на стенки бассейна и закрепление верхними сегментами;
6. Наполнение водой с параллельным разглаживанием складок на дне бассейна.
К бассейну можно сделать и дополнительное оборудование – например водные аттракционы, освещение, автоматику для укрытия бассейна.
![]() |
![]() |
|
|
![]() |
Электрические выключатели освещения, светорегуляторы (диммеры) - разновидности, способы установки и советы по выбору.
Наконец-то, поменяв квартиру, я избавилась от изобретения какого-то отечественного кулибина, с мудреным названием <выключатель с тяговым шнурком>. Что это такое, знает, наверное, каждый. Помните: чтобы зажечь свет, надо долго шарить по стене, ловить то и дело норовящий выскользнуть из рук замурзанный шнурок, свисающий с потолка, а потом, наконец-то ухватившись за него, изо всех сил дернуть? Если повезет - выключатель сработает и свет зажжется. Но так как со временем <пусковой механизм> разбалтывается, дергать приходится несколько раз:
Так вот, слава Богу, эти мучения в прошлом. Теперь я просто нажимаю на клавишу выключателя. Правда, и здесь есть свои неудобства. Во-первых, от прежних хозяев мне достались выключатели уже довольно <пожилые>. Во-вторых, наши строители по непонятным причинам устанавливают выключатели довольно высоко. Поэтому я решила сделать все, как надо. Чтобы выключатели в доме были по всем правилам современной электротехнической науки. Но сначала давайте определимся, что такое правильный, современный выключатель.
Для справки:
- Индикаторная лампочка - светящийся <глазок> на клавише выключателя;
- Контрольный выключатель - выключатель с индикаторной лампочкой, которая показывает, включен или выключен свет;
- Светорегулятор (диммер) - совмещает функции выключателя и регулятора яркости света;
- Установочная коробка - полая коробка, которую вставляют и закрепляют в стене. В ней размещают провода и внутреннюю часть выключателя.
По способу крепления проводов выключатели делятся
на выключатели с винтовым и безвинтовым зажимом
![]() |
![]() |
|
|
![]() |
В первом случае провод с помощью винта зажимают между контактными пластинами. Такой способ крепления хорош для алюминиевых проводов: в процессе работы они могут нагреваться и с течением времени потихоньку деформироваться (как говорят специалисты, начинают течь). Тогда контакт ослабевает, искрит, греется. Но достаточно лишь подкрутить винт - и все в порядке. Медные провода можно подключать безвинтовым зажимом - специальной клеммой. Быстро, просто и надежно.
По способу установки выключатели делятся
на выключатели для скрытой и открытой проводки
![]() |
![]() |
|
|
![]() |
К примеру, в дачных домиках или в старых сталинских домах провода обычно закреплены снаружи, на стене, - это и есть открытая проводка. Для нее существуют специальные <накладные> выключатели. Сейчас в городских квартирах, как правило, провода убраны в стены. А в том месте, где устанавливают выключатели, долбится небольшая полость. Кстати, если раньше выключатели держались только за счет <лапок>, упирающихся в стену, то в последнее время появились металлические крепежные пластины с отверстиями: в полость стены помещается установочная коробочка, и уже к ней шурупами крепится выключатель.
Какие бывают выключатели? Чаще всего в продаже встречаются одно- и двухклавишные выключатели, реже - трехклавишные. В Европе, например, если необходимо большее количество клавиш, группу одноклавишных или двухклавишных выключателей объединяют общей рамкой. Американцы же и южнокорейские производители не ограничиваются тремя клавишами. Они делают даже шестиклавишные выключатели, а на каждой клавише - лампочку-индикатор. Это тоже отличает их продукцию от европейских выключателей, где индикаторные лампочки бывают только в одноклавишных вариантах.
|
Возможности современных выключателей не ограничиваются включением и выключением света. Некоторые из них превратились в переключатели. Что это такое, поясню на примере. У одного моего знакомого такое устройство есть на даче. Спускаясь ночью со второго этажа на первый, он одним выключателем включает свет наверху, а другим - выключает внизу. Очень удобно. Неспециалисту отличить выключатель от переключателя по внешнему виду, конечно, трудно. Поэтому практически все иностранные производители рисуют схему подключения на внутренней стороне прибора.
![]() |
![]() |
|
|
![]() |
Замечательная штука - выключатели с подсветкой и контрольные выключатели. Правда, при внешнем сходстве они работают по разным схемам. На выключателе с подсветкой установлена уже упоминавшаяся индикаторная лампочка. Она покажет местонахождение выключателя в темной комнате или коридоре: не придется шарить руками в темноте, натыкаясь на мебель и острые углы. А вот горящая лампочка на контрольном выключателе сигнализирует: прибор (или свет) включен. Такой выключатель можно установить, например, у входа в подвал, чтобы знать, горит там свет или нет. Лампочка не светится - значит, в подвале темно, и наоборот.
К выключателям можно отнести и светорегуляторы, или диммеры. Они не только зажигают свет, но и позволяют регулировать его яркость - от слепящего сияния до приглушенного интимного освещения. Чтобы правильно выбрать нужный прибор, надо знать суммарную нагрузку, которую он может выдержать. К примеру, цифра 300 W, обозначенная на светорегуляторе, означает, что с его помощью можно менять яркость пятирожковой люстры с лампочками по 60 Вт. Однако на всякий случай советуем приобретать светорегуляторы <с запасом>.
Выключатели для ванных, саун или для установки на улице, естественно, отличаются от обычных. Чтобы они могли выдержать повышенную влажность, уличную пыль и грязь, между декоративной крышкой и внутренней частью выключателя ставят пластиковый или резиновый кожух. На одной фирме мне рассказали, что их сотрудники поставили эксперимент: дома в ванной они каждый раз поливают такой выключатель из душа. И что же? Прошел уже целый год, а выключатель до сих пор исправно работает.
Что такое антивандальные выключатели? Оказывается, сегодня есть и такие. В принципе они предназначены для общественных помещений, делают их, как правило, из ударопрочной пластмассы или из металла. Сломать или разбить такой <усиленный вариант> - задача не из легких.
Кстати, из металла делают не только антивандальные выключатели, но и дорогие, эксклюзивные серии. Но в основном корпуса выключателей - из пластмассы, а внутренняя часть - из материалов, не проводящих ток (специальных композитных материалов).
Из-за чего чаще всего ломаются эти устройства? Во-первых, из-за плохого контакта провода и контактных пластин: выключатель начинает нагреваться, искрить. В лучшем случае пластмассовый корпус может расплавиться, в худшем - возникнет пожар. Во-вторых, <долголетие> выключателя во многом зависит от механической прочности пластмассы и керамики. Например, выключатель можно случайно задеть или ударить. Хрупкий пластик не поцарапается, но может треснуть. Более пластичный выдержит удар, но со временем поцарапается. А плохая керамика, бывает, трескается практически сразу, еще при монтаже.
Как же выбрать хороший выключатель? Вот несколько простых советов.
Внимательно осмотрите выбранный выключатель. На внутренней стороне обязательно должны быть указаны значения силы тока и напряжения, на которые он рассчитан, а также значок стандарта качества страны, где он произведен. На отечественных выключателях или на упаковке импортных должен стоять знак нашего Ростеста - это своего рода гарантия государства от возможных неприятностей.
Разницу между <кондовым> дешевым выключателем и качественным изделием с четкими линиями и гладкой поверхностью увидеть в принципе нетрудно. Если же вы хотите быть на 100 процентов уверены в качестве своей покупки, приобретайте выключатели солидных фирм. Кстати, у крупных производителей выбор моделей, серий и цветов выключателей огромен, и каждый год появляется что-нибудь новенькое.
P.S. В итоге своего <маркетингового исследования> я пришла к выводу, что мне, пожалуй, подойдет система управления выключателями, которая осуществляется с пульта (очень похоже на телевизионный пульт дистанционного управления). Конечно, стоит это удовольствие недешево, но комфорт дороже.
![]() |
Существуют разные варианты клеев для плитки. Способ и условия применения, а также температура работы с ними указаны на упаковке. Для работы с клеем необходима емкость, размер которой зависит от тех задач, которые вы перед собой ставите. Для мелких ремонтных работ подойдет даже обрезанная пластиковая бутыль.
Выложите в нее необходимое количество клея и небольшими порциями добавьте воду (рис. 2). Затем с помощью шпателя тщательно перемешайте клей до получения гомогенной нетекучей массы.
![]() |
![]() |
На перемешивание не стоит жалеть времени, в противном случае в массе клея могут образоваться комки, которые могут мешать при монтаже плитки. Работать следует только со свежеприготовленным раствором. Если вам нужно приготовить большой объем плиточного клея или цементно-песчаного раствора,для его перемешивания можно воспользоваться специальным приспособлением, которое получило название «миксер». Оно представляет собой металлический шток с двумя винтовыми шнеками и круговым ограничителем (рис. 3).
Вы можете закрепить миксер в цанговом зажиме обычной бытовой электродрели (рис. 4) и приступить к смешиванию раствора. Миксер позволяет быстро и качественно перемешивать растворы и клеи объемом до 15-20 л (рис. 5).
![]() |
![]() |
Самый плохой способ сэкономить – это купить дешевые материалы. Не стоит к нему прибегать: как правило, качество таких материалов не очень высоко, а следовательно, прослужат они недолго, спровоцировав возникновение множества самых разных накладок.
Помимо того, что придется заплатить за некачественные материалы, потребуется либо постоянно подправлять дефекты, превратив свою жизнь в постоянный ремонт, либо ликвидировать результаты неудачного ремонта, покупать хорошие материалы и проводить все ремонтные работы во второй раз.
При возникновении вопроса – где хранить урожай с участка возле дома – на выручку приходит старинное изобретение наших далеких предков – погреб.
![]() |
- в погребе должна быть оптимальная для хранения продуктов температур – 2-5°С;
- относительная влажность в помещении погреба – 85-95%;
- уровень грунтовых вод – не менее чем 0,5м ниже уровня пола погреба;
- погреб должен быть темным.
Последнее условие выполнить нетрудно, основной проблемой является уровень грунтовых вод. Представим, что грунтовые воды находятся на расстоянии 3м от поверхности. Это значит, что вы можете заглубить погреб на 2,5м (т.е. сделать его заглубленным). Если грунтовые воды проходят ближе к поверхности, погреб нужно строить частично над поверхностью земли. При близких грунтовых водах строят погреб наземный.
![]() |
Достаточно прост в изготовлении земляной заглубленный погреб: котлован роется с небольшим наклоном стен вглубь (площадь пола меньше площади потолка), вокруг котлована вырывается водоотводная канава, пол делается глинобитным, стены – из досок (горбыля) или оплетаются сучьями и т.п. Потолок (из жердей, подтоварника) после глиносоломенной замазки на 30-40см засыпают землей, крыша – из горбыля, глиносоломы, каждый из двух скатов опускается до земли. Не забудьте вывести трубу для приточно-вытяжной вентиляции. Расположение лестницы в погреб: полок для продуктов; для картошки – дело вашего вкуса.
Особое внимание обратите на изготовление пола в погребе. Уложите в основание утрамбованный щебень (слоем 0,5м), пропитайте его горячим битумом. Затем слоем 0,1м уложите глинобитное покрытие, желательно с мелким кирпичным щебнем. Такой пол не будет «втягивать» влагу из нижних слоев почвы, он препятствует движению воды вверх по капиллярам почвы, поэтому в вашем погребе будет всегда сухо.
![]() |
Построить погреб можно и под гаражом, и под летней кухней, и под садовым домом. При их строительстве вы сможете использовать и бетонные кольца, и камень, и булыжники, пролитые цементным раствором.
Если у вас возникнет необходимость в строительстве погреба, поле деятельности велико: можно использовать различные материалы, строить погреб своими силами или привлекать специалистов, планировать под свои нужды его размер и высоту потолков. В любом случае будет нелишним осмотр соседских погребов – вы сможете учесть все их недостатки и достоинства при строительстве погреба на своем участке.
Страницы
- « первая
- ‹ предыдущая
- …
- 14
- 15
- 16
- 17
- 18
- 19
- 20
- 21
- 22
- …
- следующая ›
- последняя »